結構工件檢測:保障工業安全的核心防線
在航空航天、建筑工程、機械制造等領域,結構工件作為承載力的核心單元,其質量直接影響整體系統的安全性與可靠性。隨著現代工業對精度要求的指數級提升,結構工件檢測已從傳統的目視檢查發展為融合多學科技術的系統工程。通過建立包含材料性能、幾何特征、缺陷分析等維度的檢測矩陣,可精準識別工件在制造、裝配、服役各環節中的潛在風險。當前行業數據顯示,采用系統化檢測方案可使結構失效事故率降低78%,充分體現了其在工業安全體系中的戰略價值。
關鍵檢測項目體系
1. 幾何精度驗證
采用三坐標測量儀(CMM)進行微米級尺寸檢測,結合激光跟蹤儀完成大尺寸構件空間位姿分析。重點控制基準面平面度(≤0.02mm/m)、孔組位置度(±0.05mm)等關鍵參數,確保裝配兼容性。
2. 材料性能圖譜
通過光譜分析儀測定元素組成,運用顯微硬度計(HV0.5)繪制材料硬度分布云圖。同步開展拉伸試驗(延伸率≥18%)、夏比沖擊試驗(吸收功≥27J)等力學檢測,建立材料性能數字孿生模型。
3. 缺陷診斷網絡
構建多模態檢測體系:渦流檢測識別表面裂紋(靈敏度0.1mm),工業CT掃描檢出內部氣孔(分辨率5μm),相控陣超聲波定位分層缺陷(精度±1mm)。開發AI缺陷分類算法,實現缺陷類型的智能判別。
4. 連接結構評估
對焊接接頭實施X射線探傷(符合ISO17636標準),采用扭矩傳感器監控螺栓預緊力偏差(≤±5%)。開發基于聲發射技術的緊固件松動預警系統,實時監測連接結構完整性。
5. 環境耐受測試
在鹽霧試驗箱中模擬加速腐蝕(ASTM B117標準),使用熱成像儀監測高溫蠕變(800℃下變形量<0.2%)。建立振動-溫度-濕度多應力耦合試驗平臺,驗證工件在極端工況下的性能穩定性。
技術演進趨勢
當前檢測技術正朝著智能化、在線化方向快速演進:工業機器人搭載6D傳感器實現自適應檢測路徑規劃,5G傳輸技術使檢測數據實時上云,數字孿生平臺可預測工件剩余壽命。這些創新將檢測效率提升300%的同時,使質量管控從被動響應轉向主動預防。
通過構建覆蓋全生命周期的檢測體系,企業不僅能有效規避質量風險,更可積累形成工藝優化的數據資產。在智能制造2030戰略推動下,結構工件檢測正在完成從成本中心向價值創造中心的轉型升級。

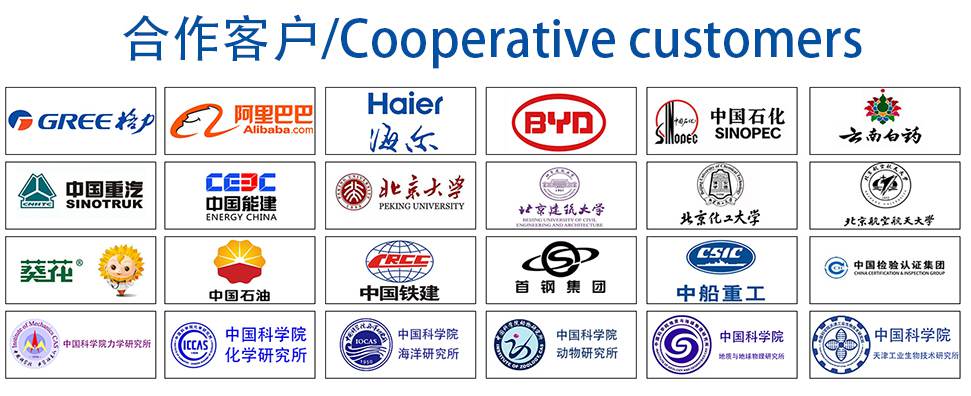