發電機組檢測的重要性與必要性
發電機組作為電力系統的核心設備,其運行狀態直接影響供電可靠性和設備使用壽命。無論是工業用電、應急備用電源還是可再生能源系統,發電機組都需要通過科學規范的檢測來確保性能穩定和安全運行。根據行業統計,70%以上的發電機組故障源于未及時發現的潛在隱患。定期檢測不僅能延長設備壽命、降低運維成本,還能避免因突發停機導致的經濟損失。尤其對于高負荷運行或老舊機組,檢測更需覆蓋機械、電氣、控制系統等多維度指標。
一、發電機組常規檢測項目
1. 外觀與基礎結構檢查:包括機組外殼完整性、固定螺栓緊固度、底座防震墊狀態等,需排查銹蝕、滲油等異常現象。
2. 絕緣電阻測試:使用兆歐表測量繞組與外殼之間的絕緣電阻,確保數值符合GB/T 755標準(通常≥1MΩ)。
3. 振動與噪聲分析:通過振動傳感器檢測軸承、曲軸等關鍵部位的振動頻率,噪聲水平應低于85dB(A)。
4. 電壓與頻率穩定性測試:空載和負載狀態下驗證輸出電壓波動范圍(±5%)及頻率偏差(≤±1Hz)。
二、專項性能檢測與診斷
1. 發電機效率測試:通過負載箱模擬實際工況,計算發電效率(一般需≥85%),識別定子/轉子損耗。
2. 控制系統驗證:檢測ATS自動切換裝置、AVR調壓器響應速度,確保過載保護、短路保護功能正常觸發。
3. 冷卻系統效能評估:監測散熱器進出口溫差(≤10℃),檢查水泵流量及風扇皮帶張緊度。
4. 燃油/潤滑系統分析:油品粘度、水分含量檢測,噴油嘴霧化效果測試,防止積碳導致功率下降。
三、智能檢測技術的應用
隨著物聯網技術的發展,紅外熱成像、在線油液監測、遠程診斷平臺逐步普及。例如:
1. 熱成像定位:通過溫度分布圖快速發現繞組局部過熱(溫升超過40℃需預警)。
2. 油液光譜分析:實時監測潤滑油金屬顆粒含量,預判軸承磨損程度。
3. 云端數據管理:整合運行參數歷史曲線,AI算法預測剩余壽命并生成檢測報告。
四、檢測周期與維護建議
根據機組類型和使用強度,建議執行以下檢測計劃:
? 日常巡檢:每日檢查油位、水位及儀表讀數
? 月度檢測:重點測試啟動電池容量、空氣濾清器阻力
? 年度全面檢測:包含繞組直流電阻測試、勵磁特性曲線分析等深度項目
對于連續運行的機組,推薦每2000小時進行潤滑油更換并同步開展性能標定。
總結
發電機組檢測是保障電力供應可靠性的基礎性工作,需結合機械、電氣、熱力多學科知識體系。通過建立標準化的檢測流程,并引入智能化診斷工具,可顯著提升設備管理水平。企業應根據機組型號、運行環境制定個性化檢測方案,同時加強技術人員培訓,構建預防性維護體系,最終實現降本增效與風險防控的雙重目標。

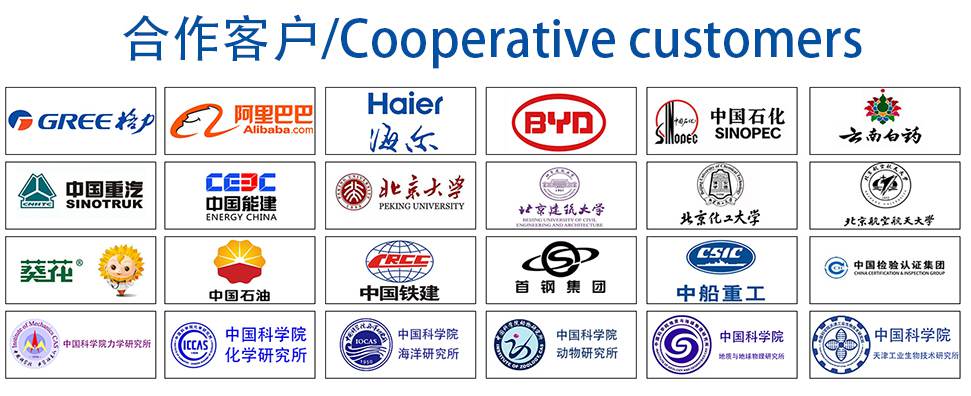