汽車罐車油氣回收系統檢測技術解析
隨著環保法規的日益嚴格和能源利用效率要求的提升,汽車罐車油氣回收系統作為危化品運輸領域的關鍵環保裝置,其性能檢測已成為行業監管的重要環節。該系統通過在裝卸過程中收集揮發性有機化合物(VOCs),有效減少大氣污染和能源浪費。目前我國已出臺GB 20952-2020等強制性標準,要求罐車每季度或每5000公里必須進行系統性檢測,以確保設備運行安全性和環保效能達標。
核心檢測項目及技術要求
1. 系統氣密性檢測
采用氮氣或空氣加壓法進行整體密封測試,要求壓力下降值在5分鐘內不超過規定閾值(通常為50Pa)。重點檢查快速接頭、呼吸閥等易泄漏部位的密封性能,使用氦質譜檢漏儀可實現0.1ppm級微量泄漏檢測。
2. 油氣回收管路壓力平衡測試
通過模擬裝車過程,驗證壓力平衡閥在0.5-1.5kPa范圍內的響應精度。使用精密壓力傳感器記錄管路壓差變化曲線,要求系統在30秒內完成壓力自動調節,防止油氣反沖或過壓泄漏。
3. 吸附裝置性能驗證
對活性炭或分子篩吸附塔進行穿透實驗,檢測動態吸附容量和脫附效率。要求吸附劑飽和時間>500小時,脫附回收率≥95%,同時檢測吸附床層溫度分布均勻性,避免局部過熱引發安全隱患。
4. 輸油管道連接可靠性檢測
使用3D激光掃描儀檢測快裝接頭同軸度誤差(≤0.3mm),進行500次插拔循環測試驗證機械耐久性。同步開展電氣導通檢測,確保防靜電接地電阻值<10Ω,防止靜電積聚風險。
5. 自動化控制單元校驗
對PLC控制系統進行邏輯測試,包括液位連鎖保護、緊急切斷響應(≤2秒)等功能驗證。使用信號發生器模擬各類故障工況,檢測系統報警準確率和應急處理程序的可靠性。
6. 安全泄放裝置檢測
重點測試呼吸閥啟閉壓力精度(誤差±10%以內)、阻火器火焰傳播特性(阻爆時間>30分鐘)。對緊急切斷閥進行爆破壓力試驗,要求動作壓力不超過設計值的1.1倍。
7. 殘留油氣濃度檢測
裝卸作業完成后,使用FID檢測器測量罐體內部VOCs濃度。要求非甲烷總烴含量≤25g/m3,苯系物濃度<1mg/m3。針對不同介質制定差異化檢測方案,如汽油罐車需額外檢測硫化物殘留。
8. 尾氣排放指標檢測
在回收裝置排氣口安裝在線監測系統,實時采集尾氣中VOCs濃度數據。按照HJ 733標準要求,非甲烷總烴排放速率≤10g/m3,檢測數據需連續存儲并支持環保部門遠程調閱。
檢測技術發展趨勢
隨著物聯網技術的應用,新型智能檢測設備可實現振動頻譜分析、紅外熱成像等無損檢測。部分檢測機構已開始運用數字孿生技術構建三維檢測模型,通過大數據分析預測系統故障周期,推動檢測模式從定期維護向預測性維護轉型。

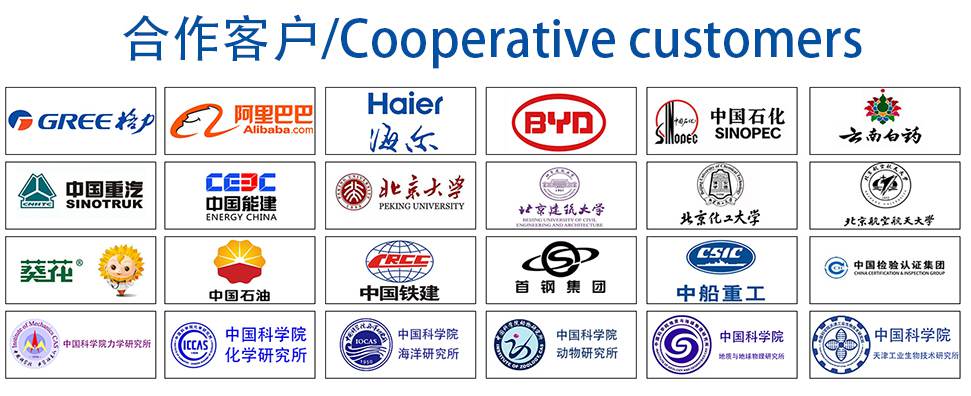