精密壓力表檢測的重要性與應用范圍
精密壓力表作為工業生產和實驗室中測量壓力參數的關鍵儀器,其準確性直接影響設備運行安全、產品質量及實驗數據的可靠性。它廣泛應用于石油化工、電力能源、制藥、航空航天等領域,用于監測管道壓力、設備承壓能力以及工藝流程控制。由于長期使用、環境因素或機械振動可能導致儀表性能下降,定期開展精密壓力表檢測是確保其計量性能符合國家標準的必要手段,也是企業質量控制體系的重要環節。
精密壓力表檢測的核心項目
1. 外觀與功能性檢查
檢測人員需檢查表殼完整性、表盤清晰度、指針靈活性及標識完整性。重點關注玻璃表面是否劃傷、刻度線是否模糊、指針是否存在卡頓現象。同時驗證儀表附件(如接頭、泄壓閥)的密封性和連接可靠性。
2. 零點誤差測試
在無壓力輸入狀態下,觀察指針是否準確指向零位。若偏離量超過JJG 49-2013《彈性元件式精密壓力表和真空表檢定規程》的允許范圍(通常≤0.5%滿量程),需通過機械調零裝置進行校準。
3. 示值誤差與線性度檢測
使用壓力標準器對儀表進行升壓和降壓測試,覆蓋10%、25%、50%、75%、100%量程點。通過計算各點實測值與標準值的偏差,判斷是否符合精度等級要求(如0.25級、0.4級)。同時分析數據線性度,確保全量程誤差分布均勻。
4. 回程誤差評估
在相同壓力點下,記錄升壓與降壓過程中指示值的最大差值。精密壓力表的回程誤差需≤允許誤差絕對值,若超標可能提示傳動機構磨損或彈性元件老化。
5. 長期穩定性試驗
將儀表持續加壓至滿量程的110%,保持4小時后恢復常壓,觀察零點漂移和量程變化。此測試可驗證彈性元件的抗疲勞性能及材料的蠕變特性。
6. 溫度影響量檢測
在高低溫試驗箱中模擬-10℃至+50℃工作環境,檢測溫度變化對示值的影響。要求溫度每變化10℃,示值誤差變化不超過基本誤差限的1/4。
檢測流程與技術要求
標準檢測流程包括:預處理(靜置24小時消除殘余應力)→目視檢查→零點校準→逐點加壓測試→數據記錄與分析→密封性驗證(1.5倍滿量程保壓試驗)。檢測環境需滿足(20±5)℃、相對濕度≤85%的要求,標準器的擴展不確定度應≤被檢表允許誤差的1/4。
維護保養與周期建議
日常使用中應避免劇烈震動、過載沖擊及腐蝕性介質接觸。根據JJG 49規定,精密壓力表檢定周期一般為1年,在惡劣工況下需縮短至6個月。檢測不合格的儀表應及時維修或更換,嚴禁通過調整量程范圍強制使用。

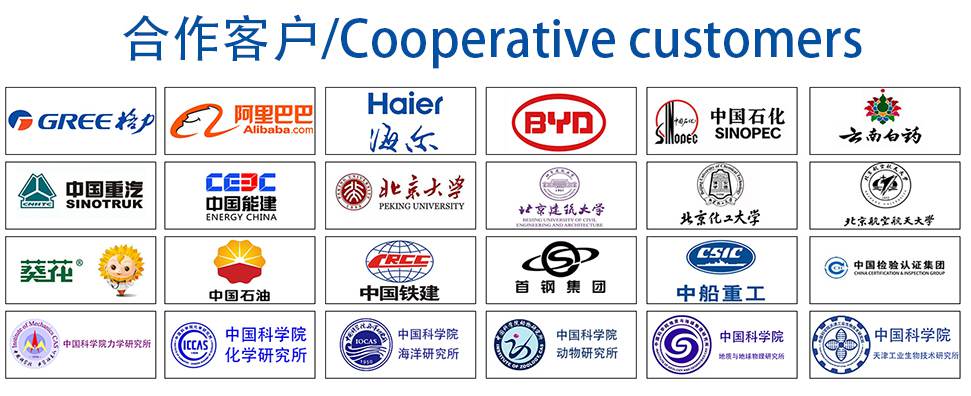