容量分析檢測:關鍵技術與應用場景解讀
容量分析檢測作為現代工業生產和科研實驗中的核心質量控制環節,主要通過定量測量物質體積、空間占比或能量存儲能力,為產品性能評估提供關鍵數據支撐。該技術廣泛應用于鋰電池制造、化工容器設計、醫療設備校準、食品包裝優化等二十余個領域,采用高精度傳感器、流體動力學模型與自動化檢測設備相結合的復合型技術路線,在保障產品安全性和合規性方面發揮著不可替代的作用。
核心檢測項目體系
完整的容量分析檢測體系包含六大關鍵指標驗證模塊,構成從基礎參數到復雜場景的全維度檢測網絡:
1. 絕對容量精度測試
采用國家計量認證的標準容器進行對比測量,運用激光掃描和重力補償技術,將檢測誤差控制在±0.05%以內。重點驗證檢測設備在滿量程、半量程及臨界值等關鍵點的線性響應特性,確保量值傳遞的可追溯性。
2. 重復性穩定性驗證
通過連續200次循環測試獲取容量離散系數,使用過程能力指數(CPK)評估設備長期穩定性。典型應用場景包括注射器容積檢測(要求CPK≥1.67)和儲氫罐體疲勞測試,可有效預測設備使用壽命。
3. 環境適應性檢測
搭建溫控精度達±0.1℃的模擬實驗艙,在-40℃至85℃溫度梯度下測試材料熱膨脹系數對容量精度的影響。針對新能源電池組等特殊應用場景,需同步進行濕度(5%-95%RH)和壓力(0.1-10MPa)多變量耦合測試。
4. 動態響應特性分析
采用高速攝像(1000fps)與粒子圖像測速(PIV)技術,捕捉液體灌注過程中氣液界面的動態變化。建立三維流場仿真模型,優化檢測系統對非牛頓流體、多相混合介質等復雜物料的測量適應性。
5. 兼容性驗證矩陣
構建包含酸/堿溶液、有機溶劑、納米流體等12類介質的測試樣本庫,評估檢測設備材質耐腐蝕性。同步測試RS485、Profinet等工業通訊協議的響應延遲,確保與自動化產線的無縫對接。
6. 數據算法驗證系統
開發基于機器學習的異常值識別算法,通過注入式測試驗證數據處理模型的可靠性。使用蒙特卡洛法進行3000次仿真實驗,確保容量計算模型在95%置信區間內的結果有效性。
當前行業前沿的智能化檢測系統已實現0.01μL級分辨率,配合數字孿生技術可構建虛擬檢測環境。隨著ASTM E542和ISO 8655等國際標準的更新迭代,容量分析檢測正朝著多模態感知、自主決策的第三代檢測系統演進,為智能制造提供更精準的質量控制方案。

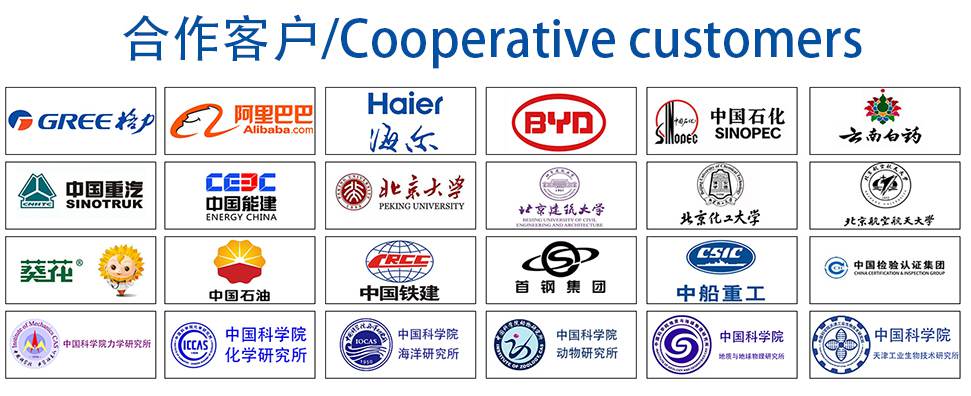