平面度檢測技術的核心原理與應用場景
平面度作為幾何公差中的關鍵指標,是衡量機械零件、電子元件和精密設備表面平整程度的重要參數。隨著智能制造和精密加工技術的快速發展,平面度檢測已從傳統的接觸式測量發展為融合光學、激光和AI算法的綜合技術體系?,F代工業對平面度的精度要求可達微米甚至納米級,尤其在半導體制造、航空航天等高精尖領域,平面度誤差可能導致設備性能下降甚至失效。
主流平面度檢測技術分類
當前主流的平面度檢測技術可分為接觸式與非接觸式兩大類。傳統接觸式檢測采用平臺檢測法,利用標準平臺與工件表面的透光間隙判斷平面度,適用于大尺寸工件粗檢。精密檢測則多使用激光平面干涉儀,通過分析干涉條紋計算表面偏差,精度可達λ/20(約30nm)。新興的激光三維掃描技術通過點云數據重構表面形態,在汽車覆蓋件檢測中實現0.05mm級精度。
智能化檢測系統的技術突破
基于機器視覺的自動化檢測系統正在革新平面度測量領域。采用高分辨率CCD相機配合多軸運動平臺,可實現300mm×300mm范圍內±1μm的重復測量精度。深度學習算法的引入使系統能自動識別表面缺陷并分類,如華為開發的SmartFlat系統可將檢測效率提升400%。工業級在線檢測設備集成溫度補償模塊,有效消除環境因素對測量結果的影響。
行業應用與標準規范
在半導體行業,晶圓平面度檢測要求達到0.1μm/m2,采用白光干涉儀配合真空吸附平臺確保測量穩定性。航空航天領域依據ASME B89.3.7標準,使用激光跟蹤儀對飛機蒙皮進行全場測量。醫療器械行業遵循ISO 2768標準,通過藍光三維掃描實現人工關節表面0.01mm級檢測。各行業普遍采用基于最小二乘法的平面度評價算法,確保測量結果符合國際規范。
技術挑戰與發展趨勢
面對異形曲面和復合材料的檢測需求,多傳感器融合技術成為研發重點。德國蔡司最新推出的COMET系統整合結構光與熱成像技術,可同時獲取幾何形貌與應力分布數據。量子測量技術的突破使原子力顯微鏡實現原子級平面度分析,為芯片光刻機臺研發提供支持。未來5年,基于5G的遠程校準系統和數字孿生檢測平臺將重構平面度質量控制體系。

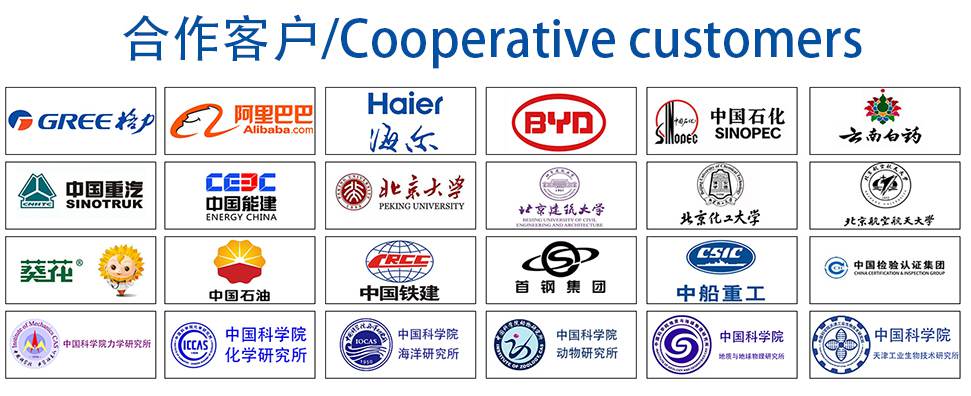