自行車輪輞檢測的重要性
作為自行車的關鍵承載部件,輪輞的性能直接關系到騎行的安全性、穩定性和舒適性。無論是公路車、山地車還是城市通勤車,輪輞在騎行過程中需要承受復雜的動態載荷,包括垂直壓力、側向沖擊力以及制動時的摩擦力。隨著材料技術的進步,輪輞的材質從傳統的鋼制發展到鋁合金、碳纖維甚至鈦合金,但無論材質如何變化,其尺寸精度、結構強度和耐久性始終是核心質量指標。通過系統化的輪輞檢測,可以有效預防因輪輞變形、斷裂或裝配偏差導致的騎行事故,同時延長零部件的使用壽命。
核心檢測項目與標準
1. 尺寸精度檢測
使用三坐標測量儀或高精度卡尺對輪輞的內徑、外徑、截面寬度進行測量,確保符合ISO 4210或EN 14764標準。重點檢查剎車邊平面度公差(通常≤0.3mm)和輪輞接縫處的對接精度,避免安裝輪胎時出現漏氣或偏擺問題。
2. 動態平衡測試
通過動平衡機模擬騎行狀態下的高速旋轉(最高達60km/h),檢測輪輞的質心偏移量。合格標準要求不平衡量小于5g·cm,超標會導致騎行時車身抖動,長期使用可能加速軸承磨損。
3. 疲勞強度試驗
在液壓伺服測試機上對輪輞施加周期性徑向載荷(一般為騎行負載的1.5倍),進行10萬次以上循環測試。試驗后輪輞不得出現裂紋或永久變形,碳纖維輪輞還需通過高溫(80℃)和低溫(-20℃)交變環境下的強度驗證。
4. 材料成分分析
采用光譜分析儀檢測鋁合金輪輞的合金配比(如6061-T6中的鎂硅含量),碳纖維輪輞需通過顯微CT掃描確認樹脂浸漬均勻性。同時通過硬度計測量表面維氏硬度(HV≥70),防止材料虛標導致的早期磨損。
5. 表面處理質量評估
使用涂層測厚儀檢查陽極氧化層或烤漆厚度(鋁輪標準為10-25μm),進行百格測試驗證附著力(脫落面積<5%)。對剎車邊需額外進行鹽霧試驗(72小時無腐蝕)和耐磨測試(500次砂紙摩擦后涂層保留率≥90%)。
智能化檢測技術發展
近年來,機器視覺系統開始應用于輪輞在線檢測,通過高幀率工業相機捕捉輪輞高速旋轉時的輪廓偏差,結合AI算法實時判斷缺陷類型。激光位移傳感器可精準測量輻條孔位分布角度誤差(允許±0.5°偏差),部分高端檢測線還能同步生成3D模型進行虛擬裝配驗證,顯著提升檢測效率與準確性。

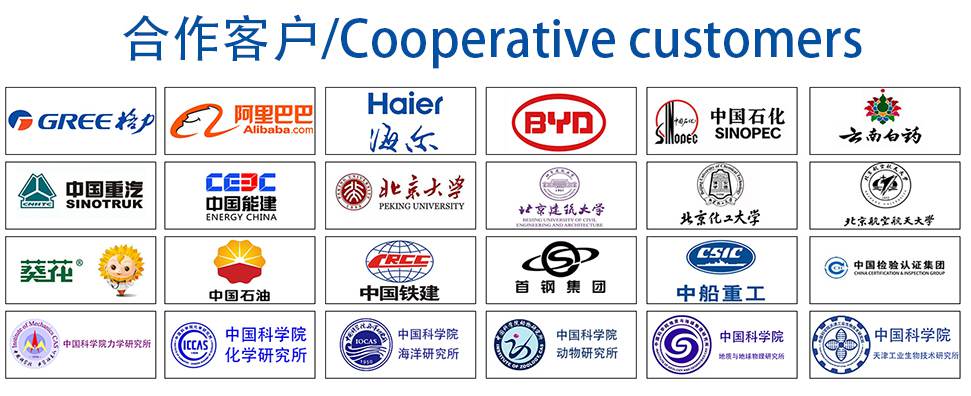