通用電子元器件(破壞性物理分析)檢測的核心作用與流程
通用電子元器件作為現代電子設備的基礎構成單元,其可靠性直接關系到終端產品的性能與安全性。尤其在航空航天、軍工裝備、醫療設備等高精密領域,元器件的微小缺陷可能導致系統級故障甚至災難性后果。破壞性物理分析(Destructive Physical Analysis, DPA)通過拆解、解剖、化學處理等手段,對元器件進行系統性結構、材料及工藝驗證,是評估其內在質量與可靠性的核心檢測方法。DPA檢測不僅能夠揭示潛在的設計或制造缺陷,還能為供應鏈質量管控提供數據支持,已成為國際標準化組織(如MIL-STD-1580、GJB 4027A)推薦的關鍵技術手段。
DPA檢測的核心項目及技術要點
1. 外部目檢與尺寸驗證
通過高倍顯微鏡或光學成像設備對元器件外殼、引腳、標識進行表面缺陷(如裂紋、氧化、劃痕)檢查,同時測量關鍵尺寸(如引腳間距、封裝厚度)是否符合設計規范。此階段需結合X射線熒光光譜(XRF)分析引腳鍍層成分,確保無鉛工藝合規性。
2. 內部結構解剖與微觀分析
采用機械切割、化學腐蝕或聚焦離子束(FIB)技術逐層剝離封裝材料,通過掃描電子顯微鏡(SEM)觀察芯片鍵合線、焊點、鈍化層等內部結構,檢測是否存在空洞、分層、金屬遷移等微觀缺陷。針對集成電路還需進行染色滲透測試(如紅墨水試驗),確認封裝粘接完整性。
3. 鍵合強度與機械性能測試
通過拉力測試機對金線/銅線鍵合點進行垂直拉伸,評估引線鍵合的抗拉強度(典型值需≥3gf);采用剪切試驗儀檢測芯片與基板的粘接強度(如環氧樹脂膠的剪切力需≥10MPa)。數據需符合JEDEC JESD22-B109等標準要求。
4. 密封性檢測與氣密性驗證
對密封型器件(如陶瓷封裝)進行氦質譜細檢漏(靈敏度達1×10?? Pa·m3/s)和氟油粗檢漏試驗,檢測封裝是否存在微米級孔隙。對于塑封器件,則需執行溫度-濕度-偏壓(THB)試驗,評估濕氣滲透對內部電路的潛在影響。
5. 材料成分與工藝逆向分析
通過能譜分析(EDS)和熱重分析(TGA)檢測封裝樹脂、基板材料的元素組成及玻璃化轉變溫度(Tg值);利用X射線衍射(XRD)解析金屬化層的晶體結構,判斷工藝參數是否偏離設計要求。針對可疑批次,可結合切片制樣技術重構生產工藝流程。
6. 失效模式與根本原因追溯
在檢測到潛在缺陷后,需通過失效分析(FA)技術定位故障根源。例如,利用紅外熱成像定位短路熱點,通過電子探針(EBIC)分析PN結漏電路徑,或采用透射電鏡(TEM)觀察柵氧化層擊穿形貌,最終形成包含失效機理、風險等級和改進建議的DPA報告。
DPA檢測的行業意義與未來發展
隨著5G通信、電動汽車等新興領域對元器件可靠性要求持續升級,DPA檢測技術正向智能化、高精度方向發展。例如,結合AI圖像識別技術實現缺陷自動分類,利用三維X射線斷層掃描(CT)重構內部結構模型。同時,基于大數據的DPA結果統計分析方法,正在為供應商質量評級和產品壽命預測提供科學依據。未來,DPA將從單一的質量檢測工具,升級為貫穿元器件全生命周期的可靠性管理平臺。

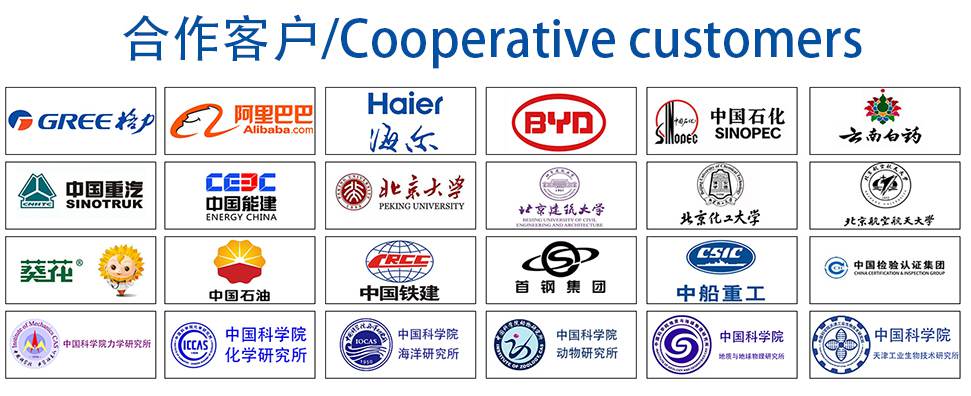