采掘機械用截齒檢測的重要性與關鍵技術
截齒作為采掘機械(如掘進機、采煤機)的核心切削部件,直接承擔著破碎巖層、煤炭等硬質物料的任務。其性能優劣直接影響設備工作效率、能源消耗及安全生產。在復雜工況下,截齒需要承受高強度沖擊、劇烈磨損和高溫腐蝕,若存在質量問題可能導致斷裂、失效甚至設備停機事故。因此,針對采掘機械用截齒的系統化檢測是保障礦山安全生產、延長設備壽命的重要環節。
核心檢測項目及技術標準
1. 材料性能檢測
通過光譜分析、金相顯微鏡等手段,驗證截齒基體材料(如42CrMo合金鋼)的化學成分、晶粒度及熱處理均勻性。重點檢測硬度梯度(齒體HRC38-45,齒尖HRC55-62)和沖擊韌性(AKU≥35J),確保材料在強沖擊載荷下的抗斷裂能力。
2. 幾何尺寸精密檢測
采用三坐標測量儀對截齒的安裝角度(65°±2°)、總長度公差(±0.5mm)、刀頭弧度半徑等關鍵參數進行數字化測量,確保與采掘機械刀盤的匹配精度,避免因裝配誤差導致的應力集中問題。
3. 表面處理質量評估
利用掃描電鏡檢測硬質合金刀頭(如YG11C)與鋼基體的釬焊結合強度,要求界面孔隙率<2%;通過鹽霧試驗驗證表面涂層(如碳化鎢涂層)的耐腐蝕性能,模擬井下高濕酸性環境下的抗銹蝕能力。
4. 動態性能模擬測試
在專用試驗臺上進行截齒旋轉切割試驗,監測不同巖層硬度(普氏系數f=4-8)下的切削力波動、溫度升高(≤300℃)及磨損速率(刀頭磨損量<0.1mm/h),構建壽命預測模型。
5. 失效模式分析
針對回收的報廢截齒,采用斷口形貌分析、能譜分析等技術,區分磨粒磨損、疲勞斷裂、熱裂紋等失效類型,為工藝改進提供數據支撐。
檢測標準的執行與創新
當前檢測體系主要參照MT/T 246-2005《采掘機械用截齒》行業標準,同時結合GB/T 23900-2009無損檢測標準。隨著智能礦山發展,部分企業已引入AI圖像識別技術實現磨損量自動判定,并運用數字孿生技術建立截齒全生命周期管理平臺,推動檢測流程向智能化、數據化方向升級。
通過上述系統化檢測,可確保截齒產品合格率提升至99.6%以上,顯著降低采掘設備故障率。未來隨著新材料(如金屬陶瓷復合材料)的應用,檢測技術將向著微觀結構分析、在線實時監測等方向發展,為礦山機械的可靠運行提供更強保障。

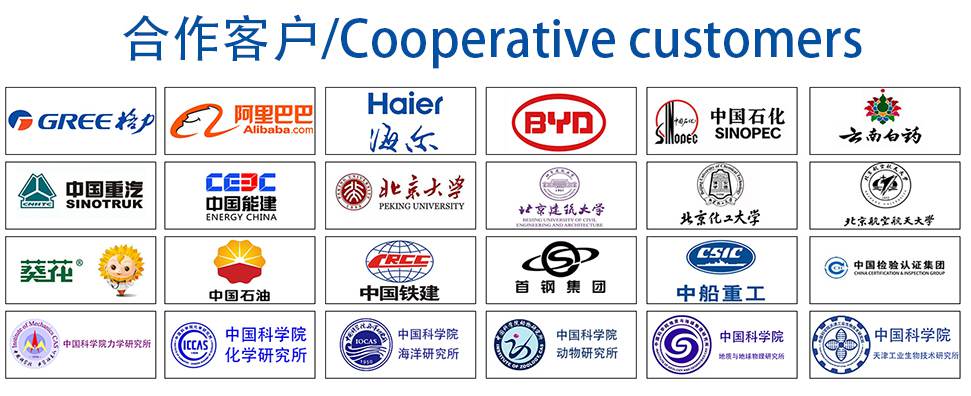