液壓系統檢測的重要性與核心內容
液壓系統作為工業設備、工程機械和航空航天等領域的關鍵動力傳輸裝置,其穩定性和安全性直接影響設備運行效率與人員安全。由于液壓系統長期處于高壓、高負荷工況下,元件磨損、油液污染、密封失效等問題可能導致系統性能下降甚至突發故障。因此,定期開展系統性檢測是預防故障、延長設備壽命的核心措施。根據行業統計,規范的液壓檢測可降低60%以上的非計劃停機風險,同時減少30%-50%的維護成本。
關鍵檢測項目清單
1. 液壓油質量檢測
通過專業儀器分析液壓油的污染度(NAS等級)、黏度、水分含量和酸值。重點檢測油液中金屬顆粒含量,判斷泵體、閥門等核心部件的磨損情況,同時檢查油液氧化程度是否超出ISO 4406標準限值。
2. 系統密封性檢測
使用壓力衰減法進行靜壓測試,檢測管路、接頭和執行器的泄漏情況。采用熒光檢漏劑輔助定位微小滲漏點,配合熱成像儀識別異常溫升區域,確保系統壓力保持能力符合GB/T 17489標準要求。
3. 壓力元件功能驗證
對液壓泵、溢流閥、減壓閥等壓力控制元件進行階梯壓力測試,記錄各設定壓力點的響應時間和穩態偏差。使用壓力傳感器矩陣監測系統壓力波動,確保動態特性滿足設備工況需求。
4. 執行機構性能檢測
針對液壓缸、液壓馬達等執行元件,測試其行程精度、輸出扭矩和速度穩定性。通過負載模擬裝置檢測帶載工況下的壓力-流量特性曲線,評估元件效率衰減程度。
5. 控制閥組響應測試
運用電液伺服測試平臺檢測比例閥、換向閥的階躍響應時間和滯環特性。重點驗證閥芯位移傳感器信號與執行器動作的同步精度,確保控制精度在±1.5%FS范圍內。
6. 溫度及振動監控
在典型工況下連續記錄系統油溫變化曲線,結合紅外熱像儀檢測局部過熱部位。安裝振動傳感器分析泵組振動頻譜,識別軸承磨損、氣蝕等早期故障特征頻率。
檢測實施注意事項
檢測前需制定詳細的測試方案,包括工況模擬程序和安全防護措施。建議采用PHM(預測與健康管理)系統進行在線監測,結合離線實驗室檢測實現全生命周期管理。檢測數據應建立趨勢分析模型,為預防性維護提供決策支持。

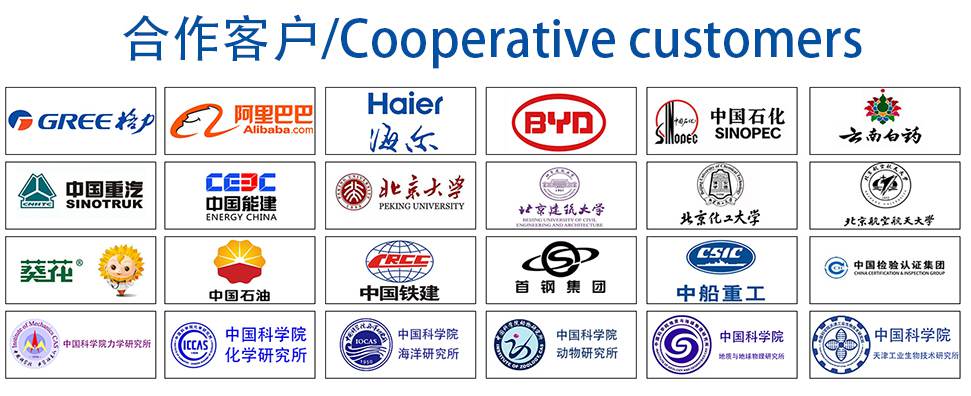