套管或油管用鋼管檢測的重要性
在石油和天然氣開采領域,套管和油管作為井下裝備的核心組成部分,承擔著支撐井壁、輸送油氣、隔離地層壓力等多重功能。由于工作環境極端復雜(高溫、高壓、腐蝕性介質等),其質量直接關系到油氣井的安全性、壽命和生產效率。因此,對套管和油管用鋼管進行系統性檢測是確保材料性能達標、避免井下事故的關鍵環節。檢測內容需覆蓋化學成分、力學性能、幾何尺寸、無損缺陷等多個維度,并嚴格遵循API(美國石油學會)、ASTM(美國材料與試驗協會)等國際標準或行業規范。
核心檢測項目及技術要求
1. 化學成分分析
鋼管的化學成分直接影響其耐腐蝕性、焊接性能和機械強度。檢測通常通過光譜分析儀對碳(C)、硅(Si)、錳(Mn)、硫(S)、磷(P)等元素進行定量測定,確保符合API 5CT等標準中的鋼級(如J55、N80、P110)要求。例如,硫、磷含量過高可能導致材料脆性增加,需嚴格控制。
2. 力學性能測試
包括拉伸試驗、沖擊試驗、硬度測試等: - 拉伸試驗:測定屈服強度、抗拉強度和延伸率,驗證鋼管在高壓環境下的抗變形能力; - 沖擊試驗:通過夏比V型缺口試樣評估低溫工況下的韌性; - 硬度測試(布氏/洛氏):反映材料耐磨性和均勻性,避免局部應力集中。
3. 幾何尺寸及表面質量檢測
使用卡尺、超聲波測厚儀、激光掃描儀等工具測量鋼管的外徑、壁厚、橢圓度、直線度等參數,確保其與設計公差一致。同時需檢查表面是否存在裂紋、折疊、結疤等缺陷,避免應力集中導致失效。
4. 無損探傷(NDT)
通過超聲波檢測(UT)、磁粉檢測(MT)、滲透檢測(PT)等技術,探測鋼管內部及近表面的缺陷: - 超聲波檢測:識別分層、夾雜、氣孔等體積型缺陷; - 磁粉檢測:發現表面或近表面裂紋; - 滲透檢測:適用于非磁性材料的表面開口缺陷檢查。
5. 螺紋加工質量檢測
套管和油管的螺紋連接部位需滿足嚴格的密封性和抗拉強度要求。檢測項目包括螺紋錐度、齒高、緊密距、螺紋表面完整性等,通常使用螺紋量規、光學投影儀等設備進行評估,確保符合API 5B標準。
6. 耐腐蝕性能試驗
針對含硫化氫(H?S)或二氧化碳(CO?)的酸性環境,需進行SSCC(硫化物應力腐蝕開裂)試驗、四點彎曲試驗等,模擬實際工況下的耐蝕能力。部分高端鋼管還需進行鹽霧試驗或電化學腐蝕速率測定。
7. 金相組織分析
通過顯微鏡觀察鋼管的晶粒度、非金屬夾雜物分布及微觀結構(如鐵素體、珠光體比例),評估熱處理工藝的合理性,避免因組織異常導致性能下降。
檢測流程與質量控制
鋼管檢測通常遵循“來料檢驗-過程監控-成品復檢”的閉環流程,部分關鍵項目(如無損探傷)需全數檢驗。檢測數據需完整記錄并實現可追溯性,同時引入第三方認證機構(如DNV、SGS)進行抽檢復核,確保檢測結果的客觀性和權威性。
結語
套管和油管用鋼管的檢測體系是石油裝備質量控制的基石。隨著智能化檢測技術(如AI圖像識別、自動化探傷系統)的普及,檢測效率和精度持續提升,為復雜油氣田開發提供了更可靠的技術保障。

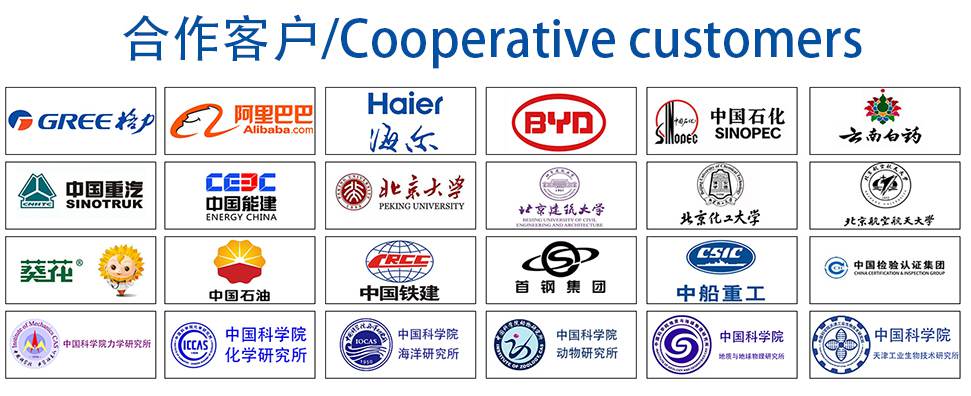