狹縫換擋定位誤差檢測的技術要點與實施流程
狹縫換擋機構作為精密機械傳動系統的重要組成部分,其定位精度直接影響著設備的運行穩定性和能量傳輸效率。在汽車變速箱、數控機床主軸箱以及工業機器人關節等場景中,換擋定位誤差超過允許范圍可能導致齒輪磨損加劇、動力傳遞中斷甚至設備損壞。定位誤差檢測通過量化分析狹縫與換擋撥叉的配合偏差,為工藝優化和設備維護提供關鍵數據支撐。隨著智能制造對傳動精度要求的持續提升,該項檢測已成為現代制造業質量控制體系中不可或缺的環節。
核心檢測項目體系
完整的狹縫換擋定位誤差檢測包含六大關鍵項目:幾何尺寸檢測通過三坐標測量儀對狹縫寬度、深度及倒角角度進行微米級測量;運動軌跡分析采用激光位移傳感器記錄換擋撥叉實際運動路徑與理論軌跡的偏差;配合間隙檢測使用塞尺和電感測微儀測定動態配合過程中的間隙變化;重復定位精度測試通過200次以上換擋循環獲取誤差分布規律;表面粗糙度檢測運用白光干涉儀評估接觸面的微觀形貌特征;溫度漂移試驗在-20℃至120℃環境倉中監測熱變形導致的誤差偏移。
動態性能檢測方法
針對高速換擋工況,引入加速度傳感器陣列和高速攝像系統對換擋沖擊進行時域分析。通過構建包含位移、速度、加速度的三維誤差模型,可準確識別0.02mm級的位置偏差。特別設計的正弦掃頻振動臺可模擬不同頻率的機械振動環境,檢測振動擾動下的定位穩定性。對于電控換擋系統,還需同步采集電磁閥電流曲線與位移傳感器數據,分析電氣延遲對機械定位的影響。
智能化檢測系統構建
現代檢測平臺整合機器視覺引導、工業機器人自動裝夾和AI數據分析模塊,實現檢測流程的全自動化。采用深度學習算法對歷史檢測數據進行模式識別,可預測誤差發展趨勢并提出維護建議?;跀底謱\生技術建立的虛擬檢測模型,能在產品設計階段預測潛在誤差源,縮短產品開發周期。檢測報告自動生成系統可輸出包含三維誤差云圖、統計過程控制(SPC)圖表和整改建議的完整分析文檔。
行業標準與精度控制
檢測過程需嚴格遵循ISO 1328-1齒輪精度標準和GB/T 17421機床檢驗規范。對于乘用車變速箱,定位誤差應控制在±0.05mm以內;高精度數控機床要求達到±0.01mm的定位精度。定期使用標準校準件進行檢測系統驗證,確保測量不確定度小于被測件公差帶的1/5。通過實施統計過程控制(SPC),建立Cpk≥1.33的穩定制程能力,可有效降低批量生產中的質量風險。

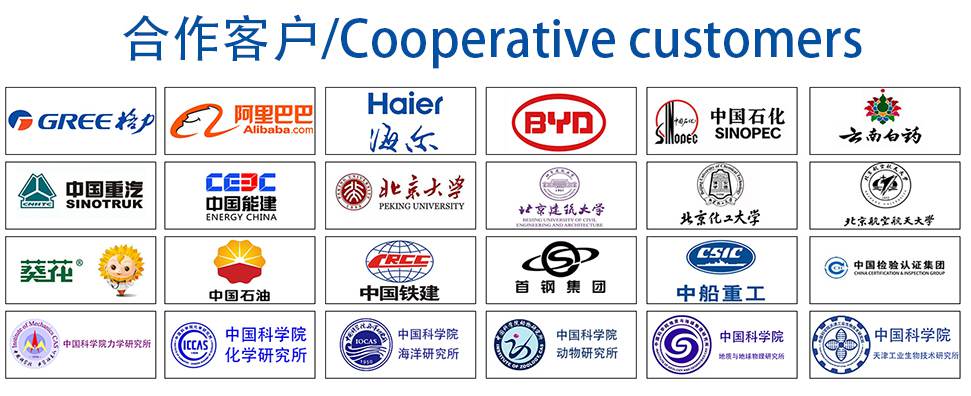