流體輸送用熱塑性塑料管道系統檢測概述
流體輸送用熱塑性塑料管道系統廣泛應用于市政供水、工業流體輸送、農業灌溉等領域,其性能直接關系到輸送效率、安全性和使用壽命。隨著材料科學的進步,聚乙烯(PE)、聚丙烯(PP)、聚氯乙烯(PVC)等熱塑性塑料管道憑借耐腐蝕、輕質高強等優勢逐步替代傳統金屬管道。然而,由于輸送介質(如水、化學品、氣體)的多樣性和環境條件的復雜性,管道系統需通過嚴格的檢測驗證其結構完整性、耐壓能力及長期穩定性。檢測項目覆蓋原材料性能、成品物理機械特性、連接密封性以及耐環境老化能力等多維度指標,是保障管道系統安全運行的核心環節。
1. 材料性能檢測
熱塑性塑料管道的基礎性能首先取決于原材料質量。檢測項目包括:熔體質量流動速率(MFR)測試,評估材料加工流動性;密度測定,驗證材料一致性;氧化誘導時間(OIT)分析,判斷抗氧化能力;炭黑含量檢測(針對黑色管道),確保抗紫外線性能。此外,通過差示掃描量熱法(DSC)分析材料的熔融溫度與結晶度,可預判管材的長期熱穩定性。
2. 物理機械性能測試
管道的力學強度是輸送系統的核心保障。檢測涵蓋拉伸強度與斷裂伸長率試驗(GB/T 8804)、液壓爆破試驗(GB/T 6111)、環剛度測試(GB/T 9647)以及簡支梁沖擊試驗(ISO 179)。其中環剛度反映管道抗外壓變形能力,而沖擊試驗模擬安裝或使用中突發外力沖擊下的抗脆裂性能。
3. 耐化學腐蝕性評價
針對輸送腐蝕性介質的特殊場景,需進行耐化學藥品浸泡試驗(ISO 4433)。通過將管材樣品浸入標準濃度的酸、堿、鹽溶液中,觀察質量變化率、尺寸變化及表面狀態,評價材料在長期接觸腐蝕介質時的耐受性。同時結合應力開裂試驗(如ASTM D5397),驗證化學環境與機械應力耦合作用下的可靠性。
4. 焊接接頭質量檢測
熱熔焊接是塑料管道系統的主要連接方式,其質量直接影響系統密封性。檢測包括:目視檢查焊口翻邊均勻性;拉伸剝離試驗(GB/T 19810)測定焊縫強度;顯微切片分析熔合界面結構完整性;氣密性試驗(ISO 13954)通過加壓檢測微滲漏。對于電熔接頭,還需驗證電阻加熱過程的溫度均勻性。
5. 長期靜液壓強度驗證
依據GB/T 18252或ISO 9080標準開展長期靜液壓試驗,通過在恒溫條件下對管材施加不同壓力等級載荷,記錄失效時間并繪制應力-壽命曲線,推算50年使用壽命下的預測強度(MRS)。該試驗是評定管道耐長期內壓能力的關鍵依據,直接影響管材設計壓力等級的確定。
6. 環境適應性測試
模擬實際使用環境開展加速老化試驗,包括:紫外老化試驗(ASTM G154)評估戶外使用時的抗光氧老化能力;熱氧老化試驗(GB/T 7141)驗證高溫環境下的性能保持率;低溫沖擊試驗(-20℃以下)檢測寒冷地區的抗脆性。對于埋地管道,還需進行土壤應力開裂試驗(ASTM D1693)和微生物腐蝕測試。
結語
流體輸送用熱塑性塑料管道系統的檢測需形成從原料到成品的全鏈條質量控制體系。隨著智能檢測技術(如超聲波探傷、紅外熱成像)的應用,檢測效率和精度持續提升。未來,綠色環保型材料的發展將進一步推動檢測標準迭代,為管道系統的安全運行提供更全面的技術保障。

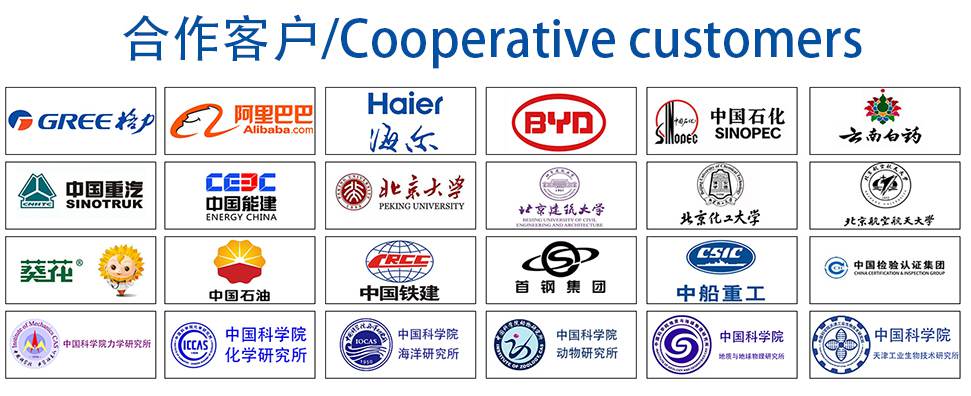