冷鐓鋼絲檢測:確保材料性能與工藝適配性的關鍵環節
冷鐓鋼絲作為制造緊固件(如螺栓、螺母、螺釘)的核心原材料,其質量直接影響產品的機械性能和加工效率。隨著汽車工業、機械制造及建筑工程領域對高強度緊固件需求的持續增長,冷鐓鋼絲檢測已成為生產鏈中不可或缺的質量控制環節。通過系統化的檢測流程,不僅可以驗證材料是否符合國標(GB/T 6478)或國際標準(如ISO 4954),更能提前發現潛在缺陷,避免冷鐓成型過程中的開裂、變形異常等問題,從而降低生產成本并保障終端產品的可靠性。
核心檢測項目詳解
1. 化學成分分析
采用直讀光譜儀對C、Si、Mn、P、S等元素進行定量檢測,確保符合牌號要求。例如SWRCH35K碳含量需控制在0.32%-0.38%,硫磷雜質需≤0.035%以保障冷鐓性能。尤其關注殘余元素(Cu、Cr等)對表面氧化皮形成的影響。
2. 力學性能測試
通過萬能試驗機開展抗拉強度(通常300-1000MPa)、斷面收縮率(≥50%)、延伸率(≥15%)測試,配備引伸計獲取精確應力-應變曲線。維氏硬度計檢測HV硬度值,確保材料具備足夠的塑性變形能力避免冷作硬化過度。
3. 表面質量檢測
使用20倍放大鏡目測檢查劃痕、折疊、裂紋等缺陷,配合渦流探傷儀檢測皮下夾雜。表面粗糙度儀測量Ra值(應≤0.8μm),線材直徑波動需控制±0.02mm以內。重點排查拉拔過程產生的螺旋紋與氧化鐵皮殘留。
4. 金相組織分析
制備縱向/橫向試樣,經4%硝酸酒精腐蝕后,通過金相顯微鏡觀察鐵素體-珠光體分布比例(理想比例為7:3),評估球化退火效果。檢查脫碳層深度(全脫碳≤1.5%線徑),晶粒度控制在6-8級以優化成型性。
5. 工藝適應性驗證
進行實物鐓粗試驗(壓縮比≥80%),模擬多工位冷鐓過程。使用高速攝像機記錄鐓制過程中是否出現表面橘皮、微裂紋等異常,配合有限元分析軟件評估材料流動均勻性,為模具設計提供數據支持。
檢測技術新發展
智能化檢測系統已實現在線直徑測量(激光測徑儀精度±0.001mm)、表面缺陷AI識別(深度學習算法識別率>98%)、超聲波探傷(可檢測Φ0.3mm以上夾雜物)等技術的集成應用。X射線熒光光譜儀(XRF)與直讀光譜儀的聯用,使元素分析效率提升60%以上。
結語
系統化的冷鐓鋼絲檢測體系貫穿從原料入庫到成品出廠的全流程,通過建立化學成分-力學性能-微觀組織-表面質量的關聯模型,可精準預測材料在高速冷成形中的表現。隨著檢測技術的智能化和標準體系的完善,冷鐓鋼絲質量控制正朝著更高效、更精準的方向持續演進。

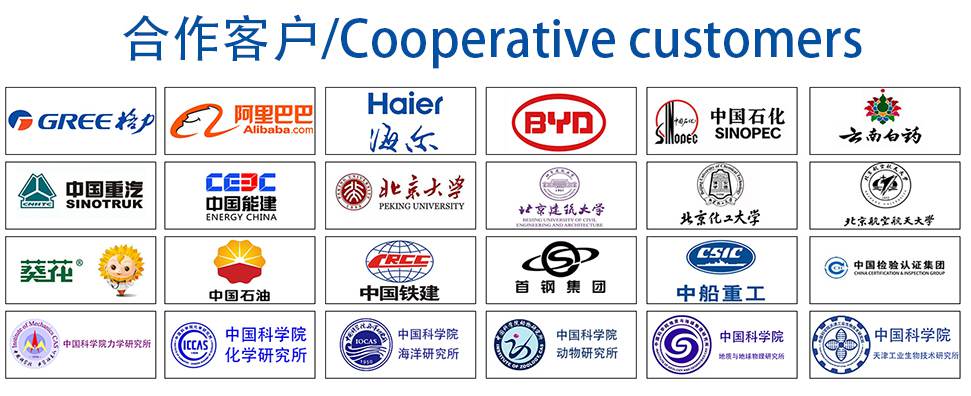