內燃機齒輪檢測的重要性
內燃機作為動力系統的核心部件,其齒輪組承擔著傳遞動力、調節轉速和扭矩的關鍵作用。齒輪的精度、強度及耐久性直接影響發動機的運行效率、噪音水平和整體壽命。在高轉速、高負荷、交變應力的工作環境下,齒輪可能出現磨損、變形、裂紋或疲勞失效等問題。因此,通過系統化的齒輪檢測項目,能夠及時識別潛在缺陷,避免因齒輪失效導致的整機故障,同時為優化生產工藝提供數據支持。現代檢測技術結合了材料科學、精密測量和數字化分析手段,形成了一套覆蓋齒輪全生命周期的質量控制體系。
齒輪幾何尺寸檢測
幾何精度是齒輪性能的基礎,檢測項目包括齒廓誤差、齒向誤差、齒距累積誤差等關鍵參數。使用三坐標測量機(CMM)進行三維建模,結合齒輪專用檢測儀測量漸開線形狀、螺旋角、分度圓直徑等指標。對于批量生產場景,會采用齒輪綜合誤差檢測儀實現快速分選,確保齒輪副的嚙合精度控制在ISO 1328或AGMA 2015標準范圍內。
表面質量與缺陷檢測
齒輪表面狀態直接影響承載能力和疲勞壽命。檢測內容包含:
1. 宏觀缺陷:通過磁粉探傷或滲透探傷檢測表面裂紋、折疊等缺陷
2. 微觀形貌:使用表面粗糙度儀測量Ra、Rz值,評估加工質量
3. 接觸斑點:通過紅丹粉著色法檢查嚙合接觸區域分布
4. 金相分析:借助電子顯微鏡觀察表層組織結構,檢測滲碳/氮化層深度
材料性能檢測
齒輪材料需滿足高強度、高韌性及耐磨性要求,主要檢測項目包括:
- 化學成分分析(光譜儀)
- 拉伸試驗測定抗拉強度、屈服強度
- 沖擊試驗評估材料韌性
- 硬度測試(洛氏/維氏硬度計)
- 殘余應力檢測(X射線衍射法)
熱處理效果驗證
熱處理工藝直接影響齒輪的機械性能,需重點檢測:
? 硬化層深度與梯度(顯微硬度法)
? 心部硬度與表面硬度匹配性
? 金相組織中馬氏體、殘余奧氏體含量
? 畸變量測量(熱處理前后尺寸對比)
動態性能測試
在模擬工況下評估齒輪實際表現:
- 動平衡測試:確保高速旋轉時振動值符合ISO 1940標準
- 疲勞試驗:在齒輪試驗臺上進行循環加載,檢測點蝕、斷齒等失效模式
- 噪聲檢測:通過聲級計分析嚙合噪音頻譜特性
結語
內燃機齒輪檢測是集精密測量、材料分析和動態測試于一體的系統工程。隨著智能制造技術的發展,在線檢測、數字孿生等新方法正逐步應用,推動檢測效率與精度的雙重提升。通過嚴格執行標準化檢測流程,可顯著提高齒輪可靠性,為內燃機的高效穩定運行提供堅實保障。

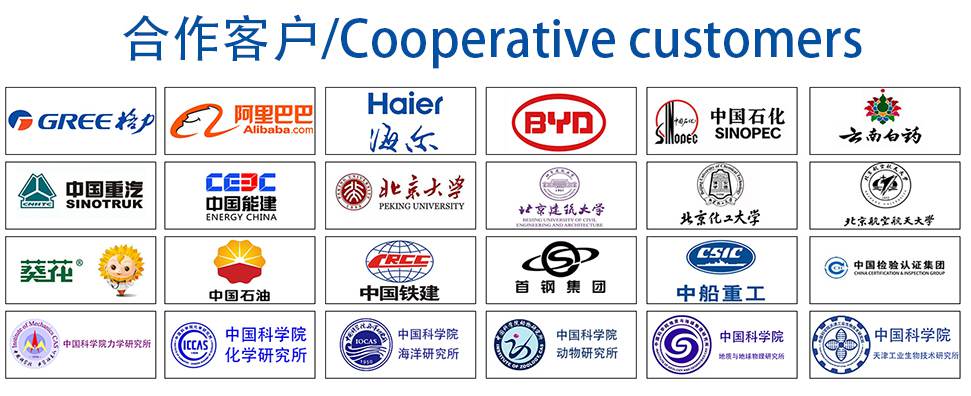