陶瓷磚自動液壓機檢測項目解析
作為現代建筑陶瓷生產線的核心設備,自動液壓機的性能直接決定了陶瓷磚的成型質量與生產效率。其檢測工作需從機械性能、控制系統到成品參數進行全方位驗證,以確保設備在高壓壓制、精準定位和快速循環等復雜工況下的穩定性。通過系統化的檢測流程,可有效規避因設備異常導致的成品開裂、尺寸偏差或能耗過高等問題,同時延長關鍵部件的使用壽命。
一、基本性能檢測
1. 壓力精度測試:采用高精度傳感器監測主缸壓力輸出,要求最大工作壓力誤差≤±2%,保壓階段壓力波動控制在設定值的±1.5%內
2. 動作同步性驗證:通過位移傳感器檢測各油缸動作時序,模具閉合階段同步誤差需<0.1mm,開模行程重復精度應達到±0.05mm
3. 循環周期穩定性:連續運行200次壓制循環,統計周期時間標準差需≤0.3秒,驗證液壓系統和PLC控制的響應速度
二、安全防護系統檢測
1. 急停裝置測試:模擬突發狀況觸發急停按鈕,驗證制動裝置應在0.2秒內完成停機,模具上升高度須立即鎖定
2. 安全光柵功能驗證:采用標準測試塊遮擋光幕,設備需在10ms內停止動作并發出聲光報警
3. 電氣防護檢測:測量設備各接地端電阻值,要求≤0.1Ω,絕緣電阻測試需≥10MΩ/500V
三、工藝參數驗證
1. 溫度場標定:在連續工作狀態下,使用紅外熱像儀監測模具溫度分布,溫差應控制在±5℃以內
2. 壓制速度測試:采用激光測速儀檢測壓制階段速度曲線,要求快下段速度誤差≤3%,工進段速度波動≤1.5%
3. 模具平行度校正:使用千分表測量上下模具四角間隙,平面度誤差需≤0.02mm/m2
四、成品質量關聯檢測
1. 磚坯尺寸檢測:通過三坐標測量儀抽檢壓制磚坯,長度/寬度公差應≤±0.3mm,厚度波動≤±0.15mm
2. 密度均勻性測試:采用γ射線密度儀掃描磚坯斷面,密度差異需<5%
3. 表面缺陷分析:借助工業相機進行視覺檢測,裂紋檢出精度達到0.1mm,邊角缺損識別率≥99%
五、檢測周期建議
根據GB/T 3810.4-2016標準,常規檢測應每500小時進行1次全面校驗,關鍵壓力傳感器需每200小時進行零點校準。新設備安裝后需進行72小時連續跑合試驗,并在首3000次沖壓周期內實施加密檢測(每8小時記錄運行數據)。
通過上述系統化的檢測方案,可確保自動液壓機保持98%以上的有效運行率,同時將陶瓷磚優等品率提升至95%以上。建議企業建立檢測數據庫,結合機器學習算法實現預測性維護,進一步降低設備故障風險。

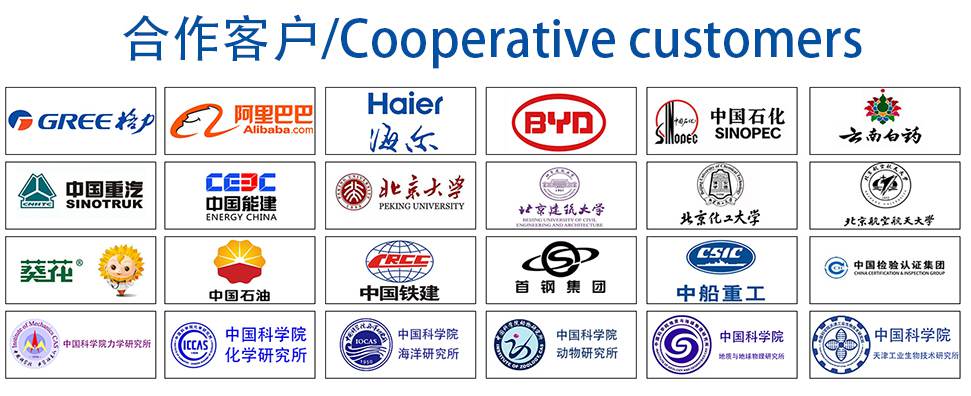