起重機械無損檢測與鋼焊縫超聲波檢測的重要性
起重機械作為工業生產和工程建設中的核心設備,其安全性和可靠性直接影響作業效率與人員安全。鋼焊縫作為起重機械金屬結構的連接關鍵部位,長期承受復雜載荷和環境影響,易出現裂紋、氣孔、未熔合等缺陷。為確保設備性能符合標準,無損檢測(Non-Destructive Testing, NDT)成為質量控制的核心手段。其中,超聲波檢測(Ultrasonic Testing, UT)憑借其高靈敏度、實時性和非破壞性特點,成為鋼焊縫缺陷檢測的首選方法。
主要檢測項目及內容
1. 焊縫內部缺陷檢測
通過超聲波探頭發射高頻聲波,檢測焊縫內部的裂紋、夾渣、氣孔等缺陷。重點分析聲波反射信號的時域和幅值特征,結合標準(如GB/T 11345-2013)判定缺陷類型、尺寸及位置,確保焊縫的連續性符合安全要求。
2. 母材與熱影響區檢測
對焊縫兩側母材及熱影響區進行掃查,檢測因焊接工藝不當導致的晶間腐蝕、微裂紋或組織不均勻問題。需結合材料厚度調整探頭頻率,確保檢測覆蓋焊接接頭全區域。
3. 焊縫厚度測量
利用超聲波脈沖回波法精確測量焊縫余高及母材厚度,驗證結構設計是否符合強度要求。尤其關注腐蝕區域或應力集中部位的厚度變化,評估剩余使用壽命。
4. 分層與夾雜物檢測
針對鋼板原材料可能存在的分層缺陷或焊接過程中引入的非金屬夾雜物,采用橫波或縱波檢測技術進行定位,防止缺陷擴展導致結構失效。
檢測流程與技術要點
檢測前需清潔焊縫表面并涂抹耦合劑,確保超聲波有效傳輸;根據材料特性選擇探頭類型(直探頭或斜探頭)及頻率(通常2-5MHz)。檢測中按預設掃查路徑覆蓋焊縫區域,實時記錄波形數據;后處理階段結合軟件分析缺陷特征,生成檢測報告。需特別注意焊縫幾何形狀對聲束傳播的影響,必要時采用TOFD(衍射時差法)或相控陣技術提升檢測精度。
標準與規范依據
檢測需嚴格遵循國家標準(GB/T 2970、GB/T 11345)、行業規范(JB/T 6061)及國際標準(ISO 17640),同時對檢測人員資質(如ISO 9712認證)和儀器校準提出明確要求,以保障檢測結果的權威性。
結語
超聲波檢測技術為起重機械鋼焊縫的質量控制提供了高效、精準的解決方案。通過系統化的檢測項目和標準化的操作流程,可有效預防因焊縫缺陷引發的安全事故,延長設備服役周期,為工業安全生產提供堅實保障。

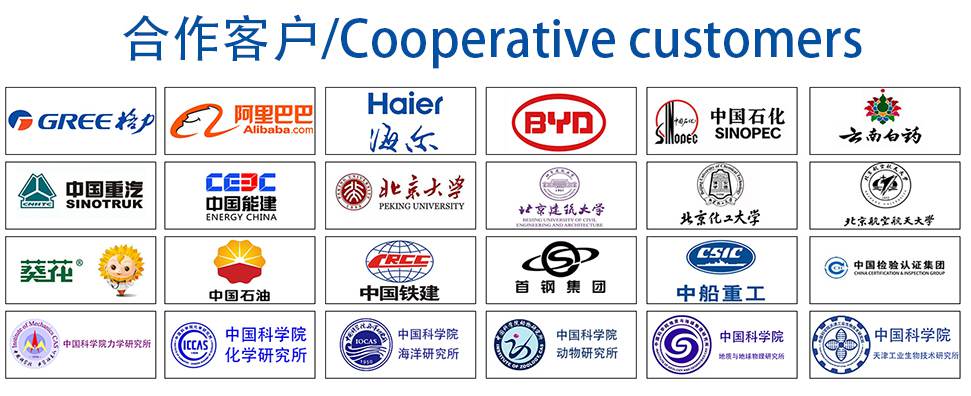