艦船液壓設備檢測體系解析
在現代化艦船裝備體系中,液壓系統作為動力傳輸的核心載體,其可靠性直接關系到船舶運行安全與作戰效能。針對液壓泵、液壓馬達、液壓閥三大核心部件,建立科學系統的檢測體系已成為船舶維護保障的重要環節。根據國際海事組織(IMO)MSC/Circ.1134號通函及國軍標GJB 6388-2008要求,液壓設備檢測項目需覆蓋性能參數、材料特性、環境適應性等28個技術維度,通過三級檢測制度確保設備在極端工況下的穩定表現。
液壓泵檢測項目
1. 容積效率檢測:采用高精度流量計對比理論流量與實際輸出流量,要求額定壓力下效率不低于92%
2. 壓力脈動測試:使用動態壓力傳感器捕捉0.1Hz-1000Hz頻段壓力波動,峰值應控制在系統壓力的±5%以內
3. 空載排量驗證:在50rpm低速工況下進行排量標定,偏差不超過公稱值的±1.5%
4. 軸向力平衡檢測:通過應變片測量軸承負載,確保最大軸向力小于設計值的85%
5. 高溫耐久性試驗:在110℃油溫條件下連續運行500小時,檢測容積效率衰減不超過2%
液壓馬達檢測項目
1. 啟動力矩測試:采用扭矩傳感器測定最低啟動壓力對應的輸出扭矩,應符合ISO 4391標準要求
2. 低速穩定性驗證:在5rpm工況下連續運轉2小時,轉速波動率應<0.5%
3. 泄漏量監測:使用同位素示蹤法檢測內泄量,每轉泄漏不超過0.1ml/rev
4. 沖擊載荷試驗:模擬螺旋槳突然卡滯工況,檢測緩沖閥響應時間≤10ms
5. 鹽霧腐蝕測試:按GJB 150.11A標準進行96小時鹽霧試驗,關鍵部件無可見腐蝕
液壓閥檢測項目
1. 閥芯換向特性:采用高速攝像系統記錄換向時間,先導式換向閥應≤25ms
2. 壓力超調量檢測:在階躍響應測試中,系統壓力超調不得超過設定值的15%
3. 微泄漏檢測:使用氦質譜檢漏儀檢測密封面,泄漏率≤1×10^-6 Pa·m3/s
4. 抗污染能力測試:在NAS 1638 8級污染油液中持續工作200小時,性能參數波動<3%
5. 振動疲勞試驗:按MIL-STD-810G方法進行三軸隨機振動測試,持續6小時無結構損傷
檢測技術創新方向
當前業內正推進基于數字孿生的預測性檢測技術,通過植入式傳感器采集壓力脈動、溫度梯度等128維特征數據,結合神經網絡算法實現故障早期預警。某型艦用液壓系統已實現關鍵部件剩余壽命預測精度達到±5%,大幅降低非計劃性維護頻次。同時,微型內窺檢測機器人、太赫茲無損探傷等新技術正在改變傳統檢測模式,可使閥體內部缺陷檢出率提升至99.7%。

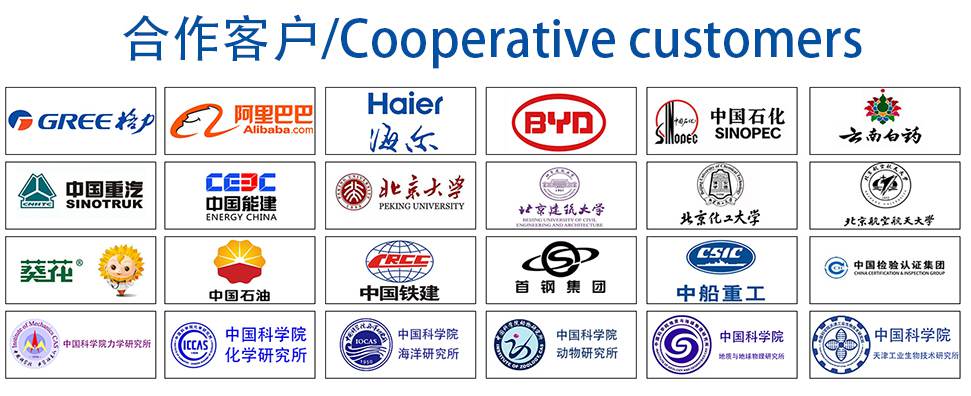