公路車輛用低壓電纜檢測的重要性
公路車輛用低壓電纜作為汽車電氣系統的核心組成部分,承擔著電力傳輸、信號控制及設備連接等關鍵功能,廣泛應用于乘用車、商用車及新能源車輛中。隨著汽車智能化、電動化趨勢的加速,電纜的安全性、可靠性和耐久性要求顯著提高。為確保車輛在復雜工況下的穩定運行,針對低壓電纜的標準化檢測成為行業規范的重要環節。根據國際標準(如ISO 6722、GB/T 25085)及車企技術要求,檢測項目需覆蓋電氣性能、機械強度、環境適應性等多個維度,以全面評估電纜質量。
關鍵檢測項目及技術要求
1. 導體性能測試
導體是電纜傳輸電流的核心部分,需通過電阻率、截面積均勻性及抗拉強度等測試。例如,依據ISO 6722標準,導體電阻偏差不得超過標稱值的±2%,同時需驗證導體在反復彎折后的斷裂伸長率,以確保其在車輛振動環境下的穩定性。
2. 絕緣與護套材料檢測
絕緣層和護套的材質直接影響電纜的耐溫、耐油及抗老化能力。檢測項目包括: - 熱老化測試:在125℃高溫下持續暴露168小時,觀察材料硬度變化與開裂現象; - 抗撕裂強度測試:模擬安裝過程中的機械損傷風險; - 耐油性測試:將試樣浸泡于汽油或機油中48小時,驗證體積膨脹率是否超標。
3. 耐候性驗證
車輛電纜需適應極端溫度、濕度及紫外線環境。通過以下測試評估其適應性: - 溫度循環測試:-40℃至+120℃間快速交變100次,檢查絕緣層龜裂情況; - 濕熱老化測試:在85℃、85%濕度下持續1000小時,評估絕緣電阻衰減率; - UV暴露測試:模擬陽光照射2000小時,檢測護套材料脆化程度。
4. 電氣性能驗證
包括絕緣電阻(≥100MΩ/km)、耐電壓(2000V/5min無擊穿)及屏蔽效能測試(針對CAN總線等高頻信號電纜),確保電磁兼容性符合ISO 11452系列標準要求。
5. 機械性能試驗
模擬實際使用場景的機械應力,如: - 彎曲試驗:以20倍電纜直徑的彎折半徑進行5000次循環; - 抗壓試驗:施加1000N壓力持續1小時,檢測絕緣層變形量; - 耐磨試驗:在鋼絲刷摩擦裝置下測試護套磨損深度。
6. 阻燃性能評估
依據UL 1581或GB/T 18380標準進行垂直燃燒測試,要求自熄時間≤60秒,炭化長度≤50mm。對新能源車輛高壓線束還需增加氧指數(OI≥32%)測試。
7. 環保與毒性檢測
針對RoHS 2.0指令,檢測鉛、鎘等重金屬含量;同時需通過VOC(揮發性有機物)釋放量測試,滿足車內空氣質量要求。
8. 標識耐久性驗證
電纜表面印刷的型號、規格等標識需通過酒精擦拭、高溫水浸等測試,確保在使用周期內清晰可辨。
檢測流程與質量管控
完整的檢測流程涵蓋原材料入廠檢驗、生產過程抽檢及成品綜合測試三個階段。車企及零部件供應商需建立ISO 17025認證實驗室,結合自動化檢測設備(如高壓測試儀、環境試驗箱)與人工目檢,實現全生命周期質量追溯。對于新能源車輛,還需增加高壓絕緣監測、EMC抗干擾等專項測試。
結語
公路車輛用低壓電纜的檢測體系是保障行車安全的核心技術屏障。隨著新材料、新工藝的應用,檢測標準將持續迭代升級。建議企業動態跟蹤IEC、SAE等行業規范,通過數字化檢測平臺優化質量控制流程,為智能網聯汽車的快速發展提供可靠保障。

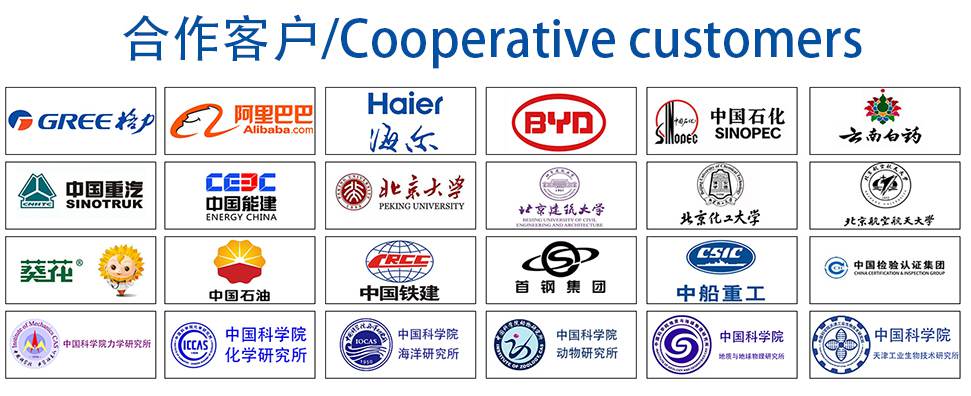