包裝機械檢測的重要性與行業需求
在食品、醫藥、日化、電子等現代制造領域,包裝機械作為生產線核心設備,其性能直接影響產品質量、生產效率及企業運營成本。隨著自動化與智能化技術的快速發展,包裝機械檢測已成為確保設備合規性、安全性和穩定性的關鍵環節。通過系統的檢測流程,企業不僅能規避因機械故障導致的生產事故,還能優化設備參數以提升包裝精度,減少材料浪費。根據ISO 9001質量管理體系及GB/T 19001國家標準規范,第三方檢測機構需對包裝機械實施全維度技術評估,為設備出廠、驗收及日常維護提供科學依據。
包裝機械核心檢測項目解析
1. 機械性能測試
包括運行速度檢測(如每分鐘包裝次數)、傳動系統穩定性分析、密封壓力測試(針對真空包裝機)以及送料機構精準度驗證。通過高精度傳感器記錄設備在滿載、空載及極端工況下的振動、噪音數據,評估機械結構的耐久性與可靠性。
2. 電氣安全檢測
依據IEC 60204-1標準,重點檢測電機絕緣電阻(需≥1MΩ)、接地連續性(接地電阻≤0.1Ω)、應急制動響應時間(≤2秒)及控制系統抗干擾能力。對伺服驅動系統進行過載保護測試,確保電路設計符合防爆、防塵、防水等級要求。
3. 材料兼容性測試
模擬實際生產環境,驗證機械與包裝材料(如PE膜、鋁箔、玻璃容器)的適配性。通過300小時連續運行試驗,檢測熱封刀頭耐腐蝕性、傳送帶抗磨損系數,防止材料殘留導致的產品污染風險。
4. 智能化功能驗證
針對配備PLC、機器視覺系統的設備,需測試自動糾偏功能的定位精度(誤差≤±0.5mm)、重量檢測模塊的重復性(RSD<0.3%),以及MES系統數據交互的實時性與準確性。通過注入模擬故障信號,檢驗設備自診斷系統的報警響應機制。
5. 環境適應性試驗
在溫濕度試驗箱中模擬-10℃至50℃極端環境,檢測機械潤滑系統效能、熱收縮爐溫控精度(波動≤±1.5℃)及電子元件的工作穩定性。鹽霧測試(48小時)可評估金屬部件在潮濕環境的防銹能力。
檢測流程標準化建設
專業檢測機構采用三級檢測體系:出廠前完成72小時空載跑合試驗,現場安裝后進行負載性能校準,每季度執行預防性維護檢測。運用激光干涉儀、扭矩測試儀等齊全設備,結合大數據分析平臺,生成包含設備OEE(整體設備效率)、MTBF(平均無故障時間)等關鍵指標的檢測報告,為企業設備管理決策提供數據支撐。

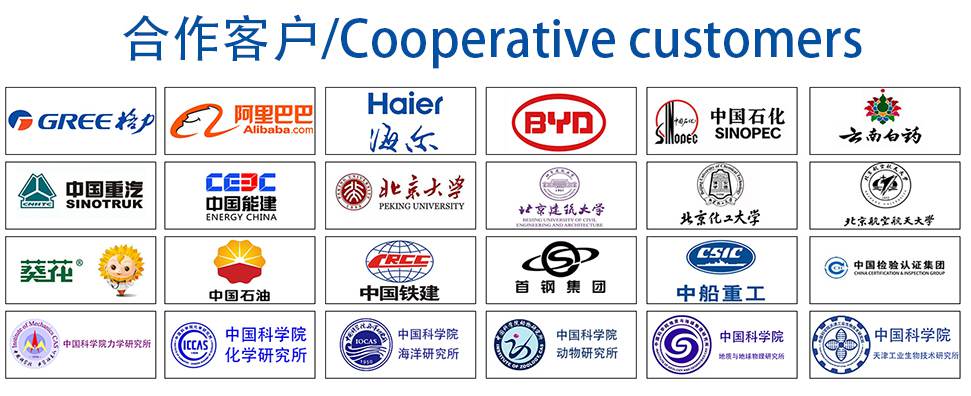