硬巖反擊式破碎機檢測的必要性與核心內容
硬巖反擊式破碎機作為礦山、建材、冶金等行業中處理高硬度物料的關鍵設備,其運行效率和可靠性直接影響生產線的穩定性和經濟效益。由于長期處于高負荷、高磨損的工況下,設備的轉子系統、反擊板、軸承、傳動裝置等核心部件易出現疲勞損傷、裂紋或變形,進而導致產能下降、能耗升高甚至突發停機事故。因此,定期開展系統性檢測是保障設備安全運行、延長使用壽命、優化工藝參數的重要手段。
核心檢測項目及技術要點
1. 轉子系統綜合檢測
轉子作為反擊破的動力核心,需重點檢測以下內容:
- 轉子動平衡測試:采用激光動平衡儀測量轉子偏重,確保振幅≤0.2mm/s,避免因失衡引發劇烈振動;
- 板錘磨損量分析:使用卡尺測量板錘厚度,當單邊磨損超過原尺寸30%或存在貫穿性裂紋時需更換;
- 轉子軸徑向跳動:千分表檢測軸向跳動應≤0.05mm/m,超差需校正或更換主軸。
2. 反擊板與襯板磨損評估
通過三維掃描或磨損模板對比法,量化反擊板工作面磨損深度。當襯板剩余厚度低于原設計50%時,需及時翻面使用或整體更換,防止物料穿透導致機殼破損。
3. 軸承溫度與潤滑狀態監測
采用紅外熱像儀實時監測軸承溫升,正常工作溫度應≤75℃。同時檢查潤滑脂的污染度及注入量,軸承游隙需控制在0.15-0.25mm范圍內,過大會加劇振動,過小則影響散熱。
4. 出料粒度與產能標定
通過篩分實驗測定成品料級配曲線,結合電流傳感器數據反推破碎效率。當產量下降10%或粒徑合格率低于85%時,需調整反擊板間隙或檢查板錘安裝角度。
5. 結構件無損探傷
對機架、軸承座等承力部位進行磁粉探傷(MT)或超聲波探傷(UT),重點排查焊接區域及應力集中點的隱性裂紋,發現深度≥3mm的缺陷需進行補焊修復。
檢測周期與維護建議
建議按以下周期實施分級檢測:每日檢查潤滑系統與異響,每周測量振動值,每季度開展全面性能測試,每年進行解體大檢。通過建立設備健康檔案,結合工況數據優化維護策略,可降低30%以上的非計劃停機風險。

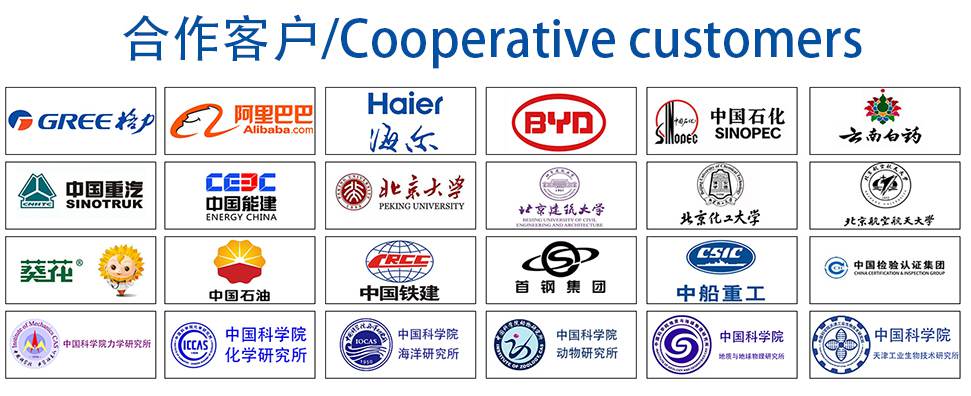