不含氣液體瓶裝生產線檢測的關鍵項目與流程
在食品、飲料、日化等行業中,不含氣液體(如純凈水、果汁、食用油、乳制品等)的瓶裝生產線對產品質量與安全性要求極高。為確保生產效率和產品合規性,生產線需進行系統性檢測,涵蓋設備性能、包裝密封性、灌裝精度、衛生安全等多個環節。檢測過程需嚴格遵循國家標準(如GB 14881《食品生產通用衛生規范》)及行業規范,同時結合自動化技術實現高效監控。
核心檢測項目分類
1. 容器完整性檢測
包括瓶身外觀檢查(裂紋、變形)、瓶口平整度檢測,以及瓶蓋與瓶口的適配性測試。通過視覺檢測系統或人工抽檢,確保容器無缺陷,避免灌裝后泄漏或污染。
2. 灌裝精度與液位控制
使用高精度流量計或稱重傳感器,實時監測每瓶液體的灌裝量,誤差需控制在±1%以內。同時,液位一致性需通過光電傳感器或圖像分析技術驗證,確保標簽標示容量與實際一致。
3. 封口密封性測試
針對瓶蓋的旋緊力度、密封圈貼合度等,采用負壓檢漏儀或壓力衰減測試法。模擬運輸環境下的振動與溫度變化,檢測是否發生滲漏。
4. 微生物與異物控制
通過在線金屬探測儀、X射線檢測設備篩查異物;定期對灌裝頭、管道、儲罐進行微生物采樣(如ATP熒光檢測),確保清潔度符合衛生標準。
5. 標簽與噴碼質量檢測
利用OCR(光學字符識別)技術核對生產日期、批次號等信息準確性,同時檢查標簽位置、粘合強度及印刷清晰度,避免信息缺失或脫落。
自動化檢測技術的應用
現代生產線普遍集成PLC控制系統、機器視覺和物聯網(IoT)技術,實現實時數據采集與異常報警。例如,智能攝像頭可同步完成瓶身缺陷、液位高度、標簽貼附等多目標檢測,效率較人工提升80%以上。檢測數據云端存儲并生成報告,便于質量追溯與工藝優化。
檢測標準與合規性管理
企業需定期校準檢測設備(如壓力表、傳感器),并通過第三方認證(如ISO 22000、HACCP)。針對出口產品,還需符合FDA(美國)或EU 1935/2004(歐盟)等國際法規,重點關注材料遷移測試與化學殘留限值。
不含氣液體瓶裝生產線的檢測既是質量保障的核心,也是企業降本增效的關鍵。通過科學的檢測體系與智能化技術,可最大限度降低人為誤差,提升產品市場競爭力。

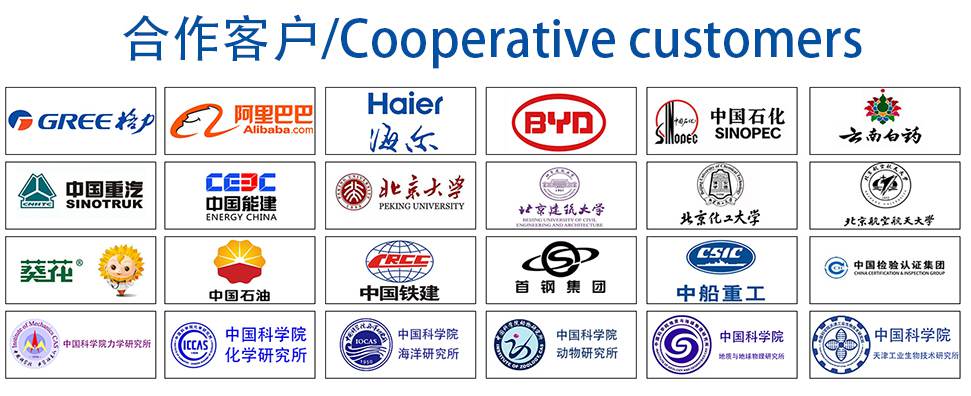