動力用空氣壓縮機(站)經濟運行與節能監測檢測體系概述
動力用空氣壓縮機(站)作為工業生產中的核心供能設備,其運行效率直接影響企業能耗成本和碳排放水平。據統計,空壓系統能耗約占工業總用電量的10%-40%,其中因設備老化、管理不當造成的能源浪費高達30%以上。構建科學的經濟運行與節能監測檢測體系,已成為實現"雙碳"目標背景下工業企業節能改造的關鍵環節。通過定期檢測與能效評估,可精準識別設備運行缺陷、管網泄漏損失、余熱回收不足等問題,為企業制定節能方案提供數據支撐。
基礎運行參數監測項目
基礎參數檢測包括:機組輸入電壓/電流波動監測(±5%標準限值)、排氣壓力穩定性檢測(波動范圍≤0.05MPa)、產氣流量與理論值偏差分析(允許誤差±3%)、潤滑油溫度監控(70-90℃最佳區間)。采用智能傳感器實時采集數據,通過DCS系統進行趨勢分析,避免因參數偏移導致的能效下降。
比功率與能效等級檢測
按照GB19153-2019《容積式空氣壓縮機能效限定值及能效等級》要求,需定期檢測機組比功率(kW/m3/min)。一級能效機組比功率≤6.2,三級能效機組≤7.8。檢測時需同步記錄環境溫度、進氣壓力等修正因子,通過實測值與標稱值對比,判斷設備能效衰減程度。
管網系統綜合檢測
包含儲氣罐排水性能測試(自動排水閥啟閉周期≤30分鐘)、管道壓降檢測(主管道壓損≤0.05MPa/100m)、末端用氣匹配度分析。采用熱成像儀掃描管網接頭,配合超聲波檢漏儀定位泄漏點(泄漏量超過總產氣量15%需緊急處理)。
熱回收系統效能評估
對余熱回收裝置進行熱力學檢測,包括換熱器溫差檢測(ΔT≥40℃為合格)、熱水產出量計量(回收率≥60%)、熱交換效率計算(≥75%)。通過能流圖分析,驗證熱回收系統對整體能效的提升貢獻值。
智能控制與能耗管理
檢測集中控制系統響應時間(≤2秒)、多機聯控邏輯合理性、用氣需求預測準確性。評估智能預警系統對異常工況(如過載、喘振)的識別率,建立基于EMS系統的能耗KPI指標體系,實現噸產品壓縮空氣單耗的動態管控。
周期性檢測與維護管理
制定年/季度檢測計劃,包括:氣閥密封性檢測(泄漏量≤3%)、傳動系統振動分析(振幅≤0.08mm)、電機能效復測(效率下降≤2%)。通過建立設備健康檔案,結合檢測數據優化維保策略,延長設備高效運行周期。
通過上述系統性檢測項目的實施,企業可實現空壓系統綜合能效提升15%-25%,年運維成本降低20%以上,同時為碳足跡核算提供可靠數據基礎。建議采用物聯網+AI的智慧監測平臺,構建覆蓋設備全生命周期的能效管理體系。

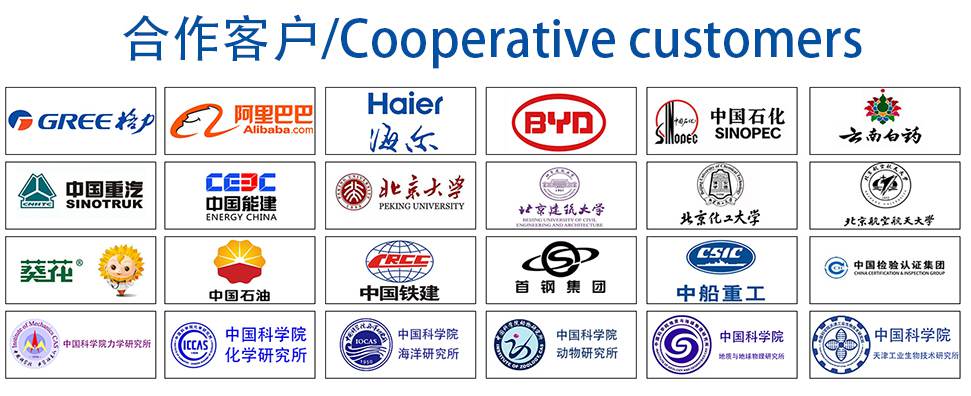