噴油單螺桿空氣壓縮機檢測的重要性
噴油單螺桿空氣壓縮機作為工業領域廣泛使用的動力設備,其運行穩定性、能效水平和安全性直接影響生產效率和設備壽命。為確保壓縮機長期高效運行,定期進行系統性檢測至關重要。通過科學規范的檢測流程,能夠及時發現潛在故障隱患,優化潤滑系統效能,避免非計劃停機,同時降低能耗和維護成本。檢測工作需覆蓋機械性能、油路狀態、密封性及控制系統等核心環節,結合行業標準和制造商技術參數進行綜合評估。
核心檢測項目及內容
1. 性能參數檢測
使用專業儀器測量排氣壓力、容積流量、比功率等關鍵指標,對比額定參數判斷性能衰減程度。重點檢測螺桿轉子與星輪的嚙合間隙,通過振動頻譜分析判斷軸承磨損情況,同時記錄運行電流波動以評估電機負載狀態。
2. 潤滑系統狀態檢測
對潤滑油進行黏度、酸值、水分含量及金屬磨損顆粒的實驗室分析,檢查油濾器壓差是否超標。采用紅外熱成像技術觀察油路分配均勻性,確保各潤滑點油膜形成質量,避免干摩擦導致部件損壞。
3. 密封性及泄漏檢測
使用超聲波檢漏儀檢查軸封、管路接頭和油氣分離器的密封效果,測量油氣混合物含油量是否超出3ppm標準。對壓力維持閥進行保壓試驗,確保停機后系統壓力下降速率符合≤0.1bar/min的要求。
4. 控制系統與安全裝置驗證
測試溫度、壓力傳感器的校準精度,驗證各級安全閥起跳壓力值(通常設定在額定壓力110%-115%)。檢查電子排污閥的啟閉響應時間,確保冷凝水排放系統工作正常,避免油液乳化。
5. 能效與熱力學分析
通過等熵效率計算評估壓縮機能耗水平,利用熱平衡法分析冷卻系統效率。重點監測排氣溫度與油溫的匹配關系,確保溫差控制在合理范圍(通常5-10℃),防止油品碳化結焦。
檢測周期與標準依據
常規檢測應每2000運行小時或季度實施一次,關鍵部件需按制造商規定更換周期進行強制檢測。執行標準涵蓋GB/T 13279-2015《一般用噴油單螺桿空氣壓縮機》、ISO 8573-1空氣質量等級要求,以及ASME PCC-2壓力系統完整性評價規范。
通過系統化的檢測流程,企業可建立完善的狀態監測體系,將事后維修轉變為預測性維護,顯著提升設備綜合效率(OEE)。建議結合物聯網技術部署在線監測系統,實現壓縮機健康狀態的實時動態管理。

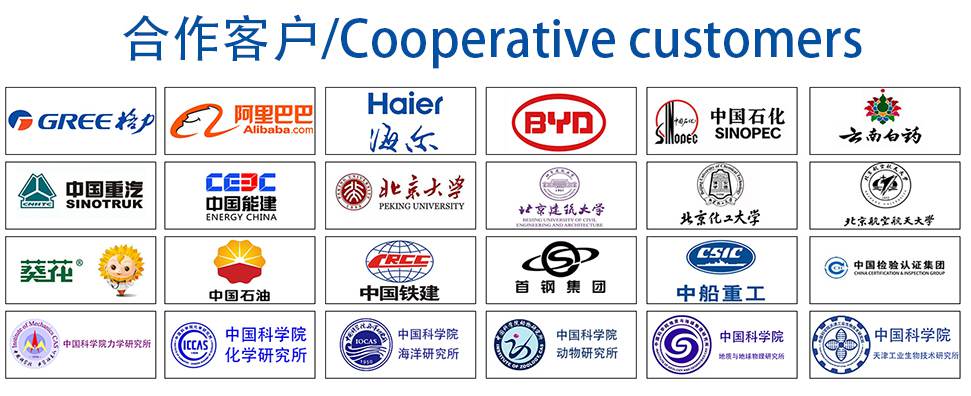