全自動一步法注拉吹成型機檢測的重要性
全自動一步法注拉吹成型機是塑料容器生產領域的核心設備,廣泛應用于食品、醫藥、日化等行業的高精度包裝瓶生產。其通過注塑、拉伸、吹塑一體化工藝,能夠高效完成從原料到成品的全流程加工。由于生產過程涉及高溫、高壓及精密控制,設備的性能穩定性、安全性和成品質量直接關系企業生產效率和成本控制。因此,針對該設備的全面檢測成為確保生產連續性與產品合格率的關鍵環節。檢測項目需覆蓋機械結構、控制系統、工藝參數及成品質量等多個維度,以識別潛在故障風險并優化工藝參數。
核心檢測項目分類與標準
1. 機械系統檢測
包括模具對位精度、開合模機構同步性、液壓/氣動系統壓力穩定性等。需使用激光測距儀檢測模具閉合間隙(誤差需≤0.05mm),通過壓力傳感器驗證油缸/氣缸輸出壓力是否滿足工藝要求(如液壓系統壓力波動值需≤±1MPa)。此外,拉伸桿與吹氣桿的同軸度需通過千分表測量,偏差應控制在±0.01mm以內。
2. 溫控系統檢測
注塑段的料筒溫度、模溫機循環水溫及吹塑段模具溫度是檢測重點。采用紅外測溫儀與熱電偶復合驗證溫控精度,要求各區段溫度波動不超過±2℃。同時需檢測加熱元件的絕緣電阻(≥5MΩ)和PID控制響應速度,確??焖龠_到設定值且無超調。
3. 電氣與安全檢測
覆蓋伺服電機扭矩輸出穩定性、PLC程序邏輯正確性及安全保護裝置(如急停按鈕、防護門聯鎖)的響應靈敏度。需通過伺服調試軟件監測電機動態負載曲線,確保其與工藝參數匹配。安全回路需進行強制觸發測試,驗證停機響應時間≤0.1秒。
4. 成品質量關聯性檢測
通過統計分析成品瓶的壁厚均勻性(壁厚差≤5%)、垂直度(偏差≤0.3mm)及密封性(氮氣保壓測試泄漏率≤0.5%),反向驗證設備工藝參數的合理性。需使用三坐標測量儀、氣密性檢測儀等專業設備完成數據采集。
5. 效率與能耗評估
記錄單模次循環時間、單位產量能耗(kW·h/kg)及原料利用率(廢料率≤3%),結合設備銘牌參數評估運行效率。同時需檢測噪聲水平(≤75dB)和振動強度(≤4.5mm/s),確保符合職業健康標準。
檢測周期與優化建議
建議每季度開展預防性檢測,并在設備大修或工藝調整后增加專項檢測。檢測數據應建立趨勢分析模型,對磨損部件(如模具導柱、液壓密封件)進行壽命預測。優化方向可包括:升級閉環溫控模塊、引入視覺定位系統提升對位精度、通過物聯網平臺實現實時狀態監控等。

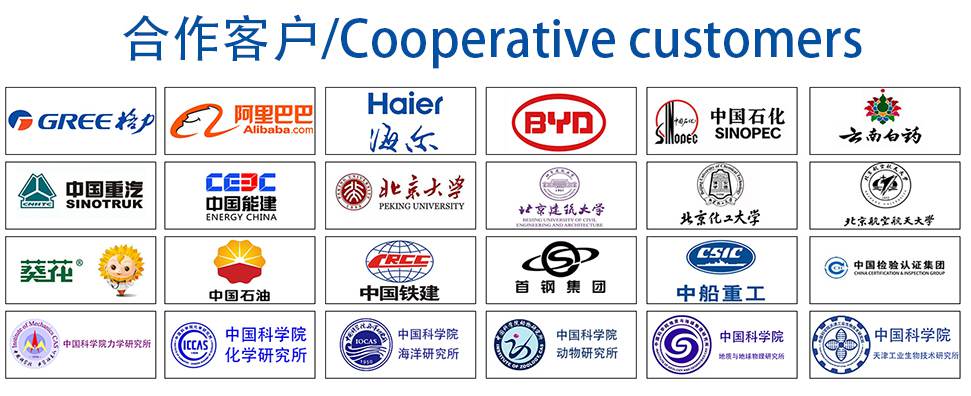