測壓裝置檢測的重要性與應用場景
測壓裝置作為工業生產、醫療設備、航空航天等領域中不可或缺的監測工具,其準確性直接關系到設備運行安全與測量數據可靠性。隨著技術發展,測壓裝置從傳統的機械式壓力表到智能數字傳感器不斷迭代,但無論哪種類型,定期檢測校準都是確保其性能的核心環節。未通過檢測的裝置可能導致壓力參數誤判,輕則影響生產效率,重則引發設備損壞甚至安全事故。因此,測壓裝置檢測已成為設備維護和質量管理體系中的強制性要求。
測壓裝置檢測的核心項目
在檢測過程中,需針對以下關鍵指標進行系統性驗證:
1. 壓力范圍校核
檢測裝置的量程覆蓋能力,包括最大工作壓力和最小分辨率,確保其適應實際工況需求。實驗室環境下通過標準壓力發生器模擬不同壓力點,對比被測裝置輸出值與標準值的偏差。
2. 精度與線性度測試
使用高精度校準儀驗證裝置在全量程范圍內的誤差率,分析其線性響應特性。非線性誤差或回差超過標準值時需進行調校或更換。
3. 密封性與耐壓性檢測
通過加壓保持試驗驗證裝置在極限壓力下的密封性能,觀察是否存在泄漏、變形或結構損壞,持續時間通常為30分鐘至2小時。
特殊功能與環境的附加檢測
1. 動態響應特性
對于高頻壓力監測場景(如液壓系統),需測試裝置的響應時間、頻率帶寬及信號穩定性,使用快速壓力脈沖發生器模擬突變工況。
2. 環境適應性驗證
在極端溫度(-40℃~150℃)、濕度(95%RH)或振動條件下測試裝置性能,確保其在復雜環境下的可靠性。
3. 信號輸出完整性
針對智能數字測壓裝置,需檢測模擬信號(4-20mA)或數字信號(RS485、HART協議)的傳輸穩定性與抗干擾能力。
檢測標準與周期管理
檢測需依據GB/T 1226-2017《一般壓力表》或ISO 國際標準執行,不同行業另有補充規范(如TSG 21-2016特種設備規范)。常規檢測周期為6-12個月,高風險領域需縮短至3個月。檢測后需出具包含修正系數、不確定度分析的技術報告,并加貼校準標識。
通過系統化的檢測流程,可最大限度降低測壓裝置失效風險,為設備安全運行和工藝優化提供數據支撐。企業應建立完整的檢測檔案,結合物聯網技術實現裝置狀態的實時監控與預測性維護。

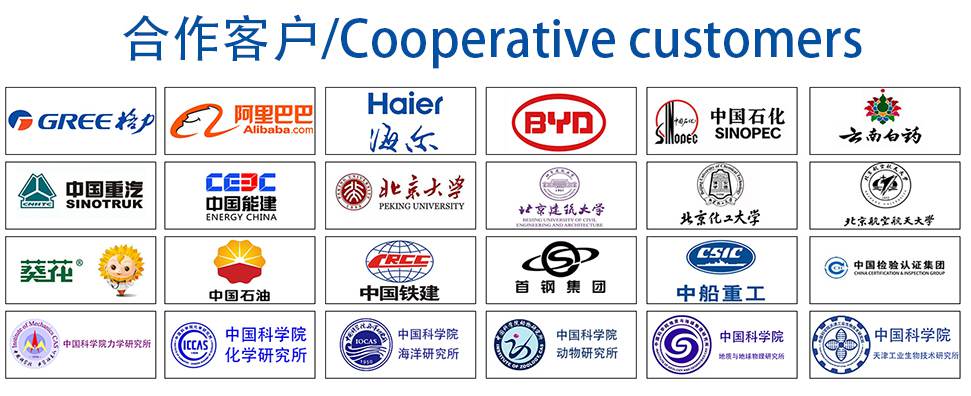