轉速相對偏差檢測的技術價值與實踐應用
在工業自動化與精密設備控制領域,轉速相對偏差檢測是評估系統運行穩定性的核心指標之一。該檢測項目通過量化實際轉速與理論設定值之間的差異程度,為設備性能診斷、質量控制及預防性維護提供關鍵數據支撐。隨著現代工業對設備運行精度要求的不斷提升,轉速相對偏差檢測已廣泛應用于電機系統、傳動裝置、渦輪機械等場景,特別是在新能源汽車電機、半導體生產線高速主軸、航空發動機等高端制造領域,其檢測結果直接關系著設備壽命、能耗效率和產品良率。
檢測原理與技術標準
轉速相對偏差的計算基于公式δ=(n_實際-n_設定)/n_設定×100%,強調相對誤差的百分比表達形式。國際電工委員會IEC 60034-30標準規定,工業電機在額定負載下運行時,轉速相對偏差應控制在±0.5%以內,而精密加工設備則要求偏差不超過±0.1%。檢測系統通常集成高精度編碼器(分辨率可達0.01°)、數字信號處理器和專用分析軟件,采樣頻率需達到被測轉速的10倍以上以保證數據有效性。
關鍵檢測項目體系
完整的轉速相對偏差檢測包含五大核心模塊:
1. 穩態偏差檢測
在恒定負載條件下連續采集3-5分鐘轉速數據,計算平均值與設定值的偏差率,評估設備基礎控制精度。需排除環境溫度波動(控制在±2℃內)對檢測結果的影響。
2. 動態響應偏差檢測
模擬負載突變(如階躍載荷變化30-50%)時的轉速恢復特性,記錄最大超調量和穩定時間。工業級伺服系統要求200ms內恢復至±0.2%偏差帶。
3. 多軸同步偏差檢測
針對紡織機械、3C產品組裝線等需要多軸聯動的設備,采用相位同步分析法,檢測各傳動軸轉速的相位差,要求多軸系統同步誤差≤0.05%。
4. 環境因素影響測試
系統評估溫濕度變化(-20℃至+60℃/20-95%RH)、振動干擾(5-2000Hz)等外部因素對轉速穩定性的影響,建立誤差補償模型。
5. 長期運行穩定性評估
通過72小時不間斷測試,監控軸承磨損、潤滑衰減等漸進性因素導致的轉速漂移,繪制偏差趨勢圖并預測維護周期。
檢測執行流程優化
標準化檢測流程包含六個步驟:①檢測系統預熱(≥30分鐘)②基準參數校準(使用標準轉速源)③傳感器安裝驗證(同軸度誤差<0.01mm)④多工況測試序列執行⑤數據有效性校驗(剔除±3σ范圍外的離群值)⑥生成包含時頻域分析的檢測報告。齊全設備已實現自動化測試,單次完整檢測周期可縮短至45分鐘。
典型應用案例分析
某新能源汽車電機廠通過引入激光多普勒測速儀(精度0.005%),將轉子動平衡檢測時的轉速偏差識別靈敏度提升3倍,使電機異響故障率下降67%。在半導體晶圓切割設備中,采用磁流體軸承配合實時偏差補償算法后,主軸轉速波動從±0.15%降至±0.03%,顯著提升切割面粗糙度等級(Ra值改進達23%)。
檢測技術發展趨勢
當前研究熱點集中在非接觸式測量(如微波干涉法)、數字孿生仿真預診斷、基于深度學習的偏差預測模型等領域。ISO/TC108正在制定新的振動與轉速綜合檢測標準,預計將引入時頻聯合分析方法,提升復雜工況下的檢測可靠性。隨著5G+工業互聯網的普及,遠程實時轉速監控系統正在形成新的設備健康管理范式。

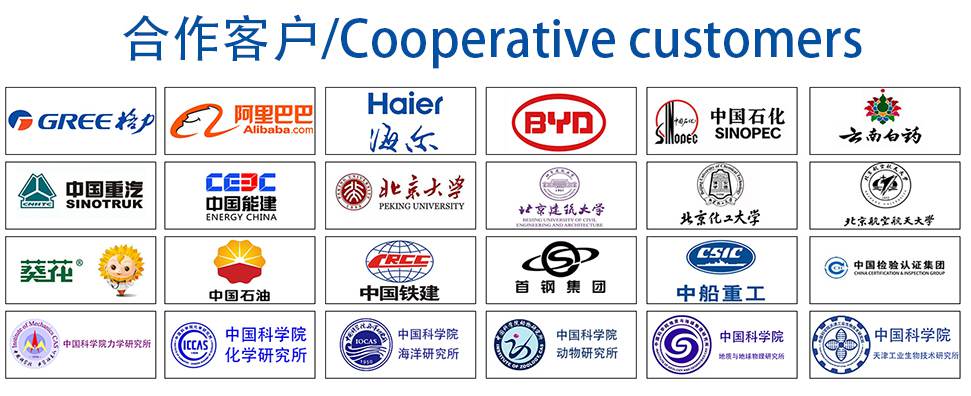