高精度加工中心檢測項目解析
在高端制造業(yè)中,高精度加工中心作為核心生產設備,其性能直接決定了零部件的加工質量與生產效率。隨著航空航天、精密模具、醫(yī)療器械等領域對零件精度要求的日益嚴苛(公差普遍要求±0.001mm級),建立科學的檢測體系已成為保障設備穩(wěn)定性的關鍵環(huán)節(jié)。通過系統性檢測不僅能驗證設備初始精度,更能通過周期性監(jiān)測預警潛在故障,避免因設備偏差造成的批量報廢損失。
一、幾何精度檢測體系
采用激光干涉儀配合電子水平儀,對X/Y/Z軸直線度、垂直度及重復定位精度進行三維空間校準,重點核查主軸端面跳動(需≤0.002mm)和徑向圓跳動誤差。通過球桿儀測試快速診斷滾珠絲杠反向間隙與圓周輪廓精度,結合花崗巖平臺驗證工作臺平面度達標情況。
二、動態(tài)性能評估方案
通過加速度傳感器監(jiān)測各軸加減速過程中的振動頻譜,利用主軸動態(tài)平衡儀檢測20000rpm高速運轉時的振動值(應控制在ISO標準G1.0級)。采用高幀率工業(yè)相機捕捉刀具換刀軌跡,驗證ATC系統定位重復性誤差是否滿足±0.005mm要求。
三、溫度補償系統驗證
構建熱變形實驗環(huán)境,在連續(xù)8小時加工周期內監(jiān)測主軸溫升曲線與熱位移量。通過布置在床身、立柱等關鍵位置的溫度傳感器陣列,驗證熱誤差補償算法的有效性。要求溫度波動±2℃時,定位精度偏差不超過補償系統設計值的30%。
四、刀具系統精度檢測
使用3D對刀儀檢測刀柄錐面接觸面積(需≥85%),配合氣動測頭驗證刀具夾持重復精度。針對HSK刀柄執(zhí)行拉刀力監(jiān)測(標準值18-22kN),并采用頻閃儀觀察高速旋轉刀具的徑向偏擺情況。
五、數控系統功能驗證
通過正弦曲線插補測試各軸動態(tài)響應特性,利用圓度測試程序檢驗圓弧插補精度。重點驗證納米級分辨率光柵尺的閉環(huán)控制效果,測試前瞻控制功能在微小線段加工中的軌跡平滑度,確保程序段處理時間≤0.5ms。
六、自動化在線檢測集成
在加工單元集成觸發(fā)式測頭與激光對刀系統,建立加工-測量-補償閉環(huán)體系。通過智能分析軟件實現SPC過程控制,要求測量數據自動上傳MES系統的延遲時間≤200ms,典型特征尺寸CPK值需穩(wěn)定在1.67以上。
通過實施上述檢測矩陣,企業(yè)可構建覆蓋設備全生命周期的精度管理體系。實踐表明,規(guī)范的檢測流程可使加工中心年故障率降低40%,刀具損耗減少25%,在提升良品率的同時顯著降低綜合運維成本,為高附加值產品制造提供可靠保障。

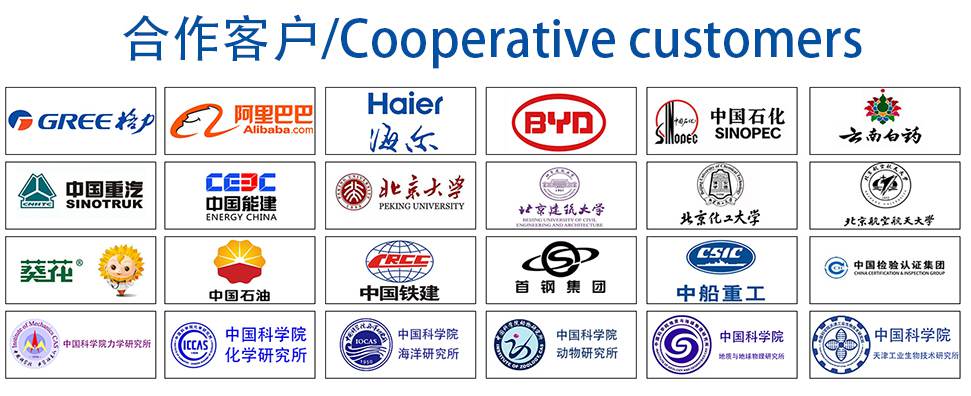