升降臺銑床檢測的要點與流程解析
升降臺銑床作為機械加工領域的核心設備,其加工精度、運行穩定性和安全性直接影響產品質量和生產效率。為確保設備長期處于最佳工作狀態,定期開展系統性檢測至關重要。檢測內容需覆蓋機床結構、運動系統、電氣控制及附屬裝置,同時需結合國家標準(如GB/T 6477-2008)和企業實際使用需求制定檢測方案。
一、幾何精度檢測
通過高精度量具對基礎參數進行測量:
1. 主軸徑向跳動檢測:使用千分表在主軸錐孔插入檢驗棒,以不同轉速測量跳動量,誤差應≤0.015mm
2. 工作臺平面度檢測:采用電子水平儀沿X/Y/Z方向測量,平面度偏差需控制在0.02mm/m范圍內
3. 導軌平行度校準:用框型水平儀對比導軌與工作臺移動軌跡的平行度,最大允差為0.04mm/1000mm
二、運動性能檢測
重點驗證機械傳動系統的協調性:
1. 進給系統重復定位精度測試:通過激光干涉儀測量各軸向移動的定位偏差,要求≤±0.005mm
2. 升降臺垂直運動同步性檢測:在滿載狀態下檢查兩側絲杠的同步誤差,不應超過0.02mm
3. 自動換刀裝置(選配)可靠性驗證:連續完成200次換刀動作,統計成功率及定位精度衰減值
三、電氣系統檢測
使用專業儀器進行電氣參數測量:
1. 主電機功率波動監測:通過電能質量分析儀記錄電機在重切削時的電流/電壓波動曲線
2. 數控系統信號響應測試:模擬加工指令驗證I/O端口響應時間,需≤0.1秒
3. 安全保護裝置功能驗證:包括限位開關、急停按鈕、過載保護等裝置的聯動響應測試
四、潤滑與冷卻系統檢測
針對關鍵部位開展專項檢查:
1. 主軸軸承溫升測試:紅外測溫儀監測連續工作4小時后的溫升情況,溫升應≤35℃
2. 潤滑油路壓力檢測:使用壓力表測量各潤滑點的油壓值,確保達到0.2-0.4MPa標準值
3. 冷卻液循環效率評估:記錄單位時間內冷卻液流量及過濾裝置的工作狀態
五、綜合加工精度驗證
通過試切件進行最終性能確認:
1. 選用45#鋼標準試塊進行端面銑削
2. 檢測加工件的表面粗糙度(Ra≤1.6μm)
3. 測量多工序加工后的尺寸鏈累積誤差(控制在IT7級精度內)
企業應建立包含預防性檢測、周期性校準和突發性故障診斷的三級檢測體系。建議每季度進行常規檢測,每年開展全面精度校準,同時結合設備使用強度適當調整檢測周期。規范的檢測流程不僅能延長設備使用壽命,更可降低因精度失效導致的廢品率,保障企業的持續生產能力。

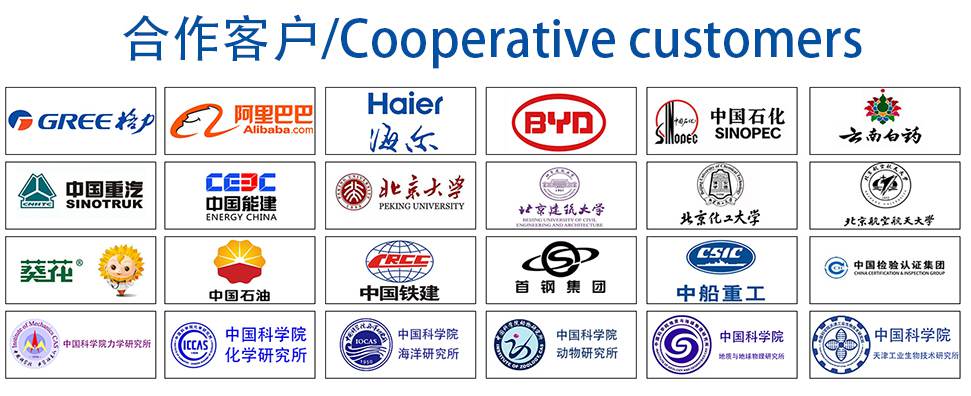