高精度臥式車床檢測:關鍵技術指標與實施流程
高精度臥式車床作為機械制造領域的核心設備,其加工精度直接影響零件質量與工藝穩定性。隨著現代工業對微米級甚至亞微米級公差要求的不斷提升,車床的綜合性能檢測已成為保障生產效率和產品質量的關鍵環節。通過系統性檢測,可及時發現床身導軌磨損、主軸跳動、進給系統誤差等潛在問題,避免因設備偏差導致的批量性加工缺陷。目前,國際標準ISO 13041和國家標準GB/T 16462系列均對數控臥式車床的檢測方法及精度等級作出明確規定,涵蓋幾何精度、動態性能、熱穩定性等十余項核心指標。
一、幾何精度檢測項目
1. 床身導軌直線度與平行度:采用激光干涉儀或電子水平儀對導軌縱向、橫向進行分段測量,誤差需控制在0.01mm/1000mm以內。
2. 主軸系統精度檢測:包含主軸徑向跳動(≤0.005mm)、端面跳動(≤0.008mm)及軸向竄動(≤0.003mm)的精密測試。
3. 刀架運動直線度:通過標準試棒配合千分表進行X/Z軸復合運動軌跡檢測,確保刀軌偏差符合H級精度標準。
二、動態性能檢測指標
1. 主軸溫升與熱變形:連續運轉4小時后,主軸前端溫升不超過25℃,徑向熱位移量需≤5μm。
2. 進給系統定位精度:使用激光干涉儀執行全行程雙向定位測試,重復定位誤差應穩定在±1.5μm范圍內。
3. 振動與噪聲測試:主傳動系統在最高轉速工況下,振動速度有效值≤2.8mm/s,噪聲級不高于75dB(A)。
三、加工精度驗證體系
通過典型試件切削實驗完成最終精度驗證:
- 圓柱試件圓度誤差:直徑≤100mm時允差0.005mm
- 端面平面度:直徑200mm范圍內≤0.008mm
- 螺紋中徑誤差:需符合ISO 1級精度標準
檢測過程需使用三坐標測量機(CMM)和表面粗糙度儀進行多維度數據采集。
四、智能化檢測技術應用
現代檢測方案已集成在線監測系統(如嵌入式傳感器網絡)和AI數據分析平臺,實現:
1. 實時監測主軸軸承預緊力變化
2. 自動補償導軌磨損引起的定位偏差
3. 預測性維護提醒功能,降低設備突發故障風險
高精度臥式車床的全面檢測應遵循"靜態檢測-動態測試-加工驗證"三位一體的評估體系,建議每500工作小時或重大工藝調整后執行系統性檢測。通過嚴格執行檢測規范,可確保設備長期保持標稱精度,同時降低加工廢品率30%以上,為企業創造顯著經濟效益。

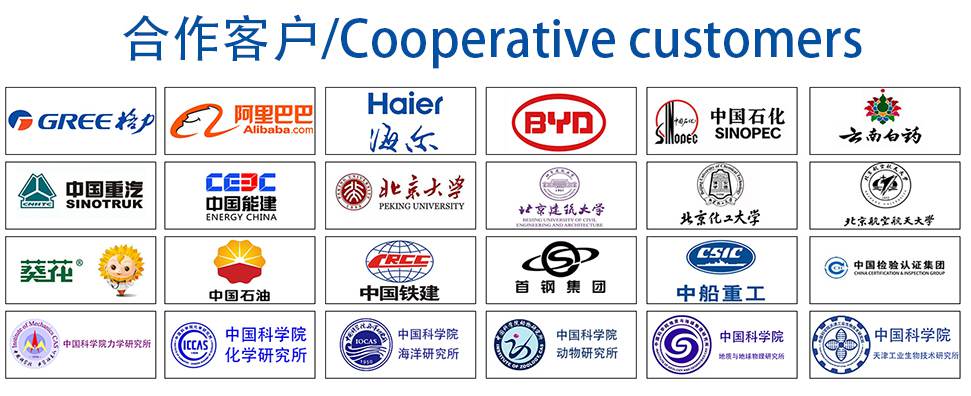