鈦及鈦合金絲檢測的重要性
鈦及鈦合金絲因其優異的強度、耐腐蝕性和生物相容性,廣泛應用于航空航天、醫療器械、化工設備及高端制造業。隨著工業需求的提升,對其性能的穩定性要求日益嚴格。檢測作為質量控制的核心環節,不僅能確保材料滿足設計標準,還能避免因材料缺陷導致的安全事故。鈦絲檢測需覆蓋化學成分、力學性能、尺寸精度、表面質量等多個維度,通過科學的檢測手段與標準規范,為產業鏈提供可靠的技術保障。
核心檢測項目與技術要求
1. 化學成分分析
通過光譜分析(ICP-OES、XRF)或化學滴定法,精確測定鈦基體中鋁、釩、鐵等合金元素的含量,確保符合GB/T 3620.1-2016等標準要求。雜質元素如氧、氮、氫需控制在ppm級,以避免晶界脆化。
2. 力學性能測試
包括拉伸試驗(抗拉強度、屈服強度、延伸率)、彎曲試驗(180°反復彎曲次數)及硬度測試(維氏/洛氏硬度)。需依據ASTM E8/E8M標準,模擬實際工況驗證材料的承載能力與塑性變形極限。
3. 尺寸與表面質量檢測
使用激光測徑儀、電子千分尺測量絲材直徑公差(±0.02mm以內),表面粗糙度需≤Ra0.8μm。借助電子顯微鏡檢查裂紋、折疊、氧化皮等缺陷,確保表面光潔度符合AMS 4951A等航空標準。
4. 耐腐蝕性評估
通過鹽霧試驗(ASTM B117)、電化學極化曲線測試,驗證在5%NaCl溶液或酸性環境下的耐蝕性能。醫用鈦絲還需模擬體液環境(如HBSS溶液)進行長期浸泡實驗。
5. 顯微組織分析
金相制樣后,采用光學顯微鏡或SEM觀察α/β相分布、晶粒度(ASTM E112)及夾雜物含量。等軸細晶組織(晶粒尺寸≤50μm)可顯著提升材料的綜合性能。
6. 無損檢測(NDT)
應用渦流檢測(EN 1711)篩查表面微裂紋,超聲波檢測(ASTM E317)定位內部缺陷(如氣孔、縮松),確保缺陷檢出率≥99%。
檢測數據的應用與趨勢
通過建立數字化檢測數據庫,可實現工藝參數的逆向優化。目前,AI驅動的缺陷智能識別技術已逐步應用于在線檢測系統,結合3D輪廓掃描儀,將檢測效率提升40%以上,推動鈦絲制造向高精度、智能化方向發展。

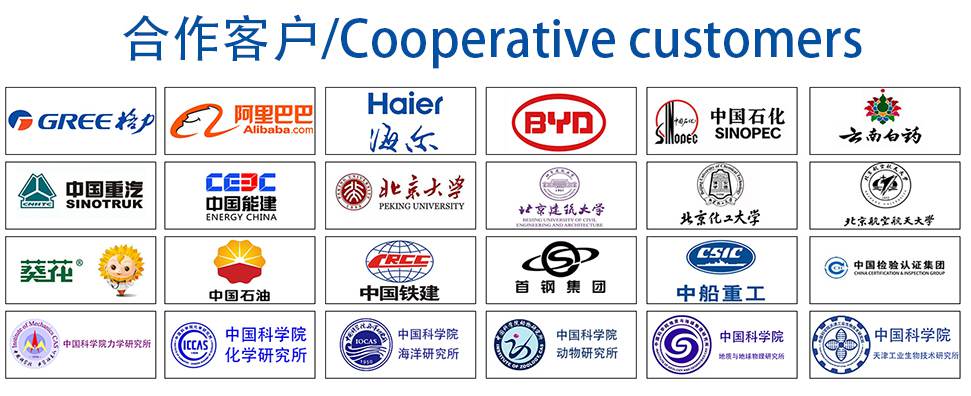