空氣壓縮機組及供氣系統檢測的重要性
空氣壓縮機組及供氣系統作為工業生產的核心動力源,廣泛應用于制造業、能源、化工、醫療等領域。其運行效率、安全性和穩定性直接關系到生產流程的連續性和設備壽命。由于系統長期處于高壓、高溫和高負荷工況,內部組件易出現磨損、泄漏、積碳等問題,可能導致能源浪費、設備故障甚至安全事故。因此,定期開展系統性檢測是保障設備高效運行、降低運維成本、滿足環保與安全規范的必要手段。
核心檢測項目及技術要求
1. 機組運行參數監測
包括壓縮機排氣壓力、溫度、電流、振動值等關鍵參數的實時采集與分析,需對照設備銘牌額定值及行業標準(如GB/T 15487-2015)進行偏差評估。使用紅外測溫儀、振動分析儀等工具可精準識別軸承過熱、轉子不平衡等隱患。
2. 安全閥與壓力容器檢測
依據TSG 21-2016《固定式壓力容器安全技術監察規程》,重點檢查安全閥啟閉壓力、密封性能及校驗周期,同時對儲氣罐進行壁厚測量(超聲波測厚儀)和焊縫探傷檢測,確保壓力容器符合承壓要求。
3. 冷卻系統效能評估
通過檢測冷卻水流量、進出水溫差(建議溫差≤10℃)及散熱器表面清潔度,評估換熱效率。風冷系統需檢測風扇轉速、翅片堵塞情況,避免因散熱不良導致的機組高溫停機。
4. 氣路系統泄漏檢測
采用超聲波檢漏儀或皂泡法對管道、法蘭、閥門等連接部位進行氣密性檢測。根據ISO 8573-1標準,系統泄漏量應控制在額定排氣量的3%以內,超標泄漏不僅增加能耗,還會縮短壓縮機加載周期。
5. 壓縮空氣品質分析
使用露點儀、油分檢測儀等設備檢測出口空氣的含水量(壓力露點≤-20℃)、含油量(Class 1級≤0.01mg/m3)及顆粒物濃度(Class 2級≤1μm),確保符合ISO 8573潔凈度等級要求,避免對氣動元件造成污染。
6. 控制系統功能驗證
模擬測試壓力開關、溫度傳感器、聯鎖保護裝置的響應精度和及時性,重點校驗壓力容器的自動泄壓功能與電機過載保護機制,確??刂七壿嫹螱B 50029-2014設計規范。
檢測周期與維護建議
常規檢測應每季度實施1次,關鍵部件(如安全閥、壓力表)需按法規要求強制年檢。建議建立設備健康檔案,結合運行數據分析預測性維護節點。對于老舊機組,檢測頻率應提高至每月1次,重點關注缸體磨損量(塞尺測量)與閥片密封性等衰退指標。通過科學的檢測與維護,可使系統能效提升15%-30%,故障率降低40%以上。

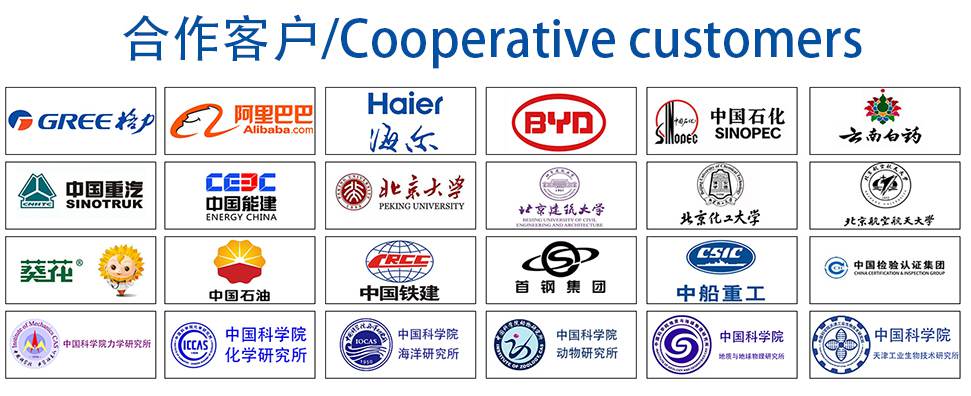