傳動軸用電焊鋼管檢測的重要性
傳動軸作為動力傳輸的核心部件,廣泛應用于汽車、工程機械及工業設備中。其中,電焊鋼管因其高強度、輕量化及良好的加工性能,成為傳動軸制造的關鍵材料。然而,鋼管的質量直接關系到傳動軸的安全性、耐久性和工作效率。因此,對電焊鋼管進行系統化檢測是保障產品性能的重要環節。通過科學的檢測手段,可有效識別材料缺陷、焊縫質量隱患及尺寸偏差等問題,從而避免因鋼管質量問題導致的傳動軸斷裂、振動異常或壽命縮短等風險。
主要檢測項目及標準
1. 材料力學性能檢測
包括拉伸試驗、彎曲試驗和沖擊試驗,評估鋼管的抗拉強度、屈服強度、延伸率和沖擊韌性。參照GB/T 228.1《金屬材料 拉伸試驗》標準,確保材料滿足傳動軸在動態負載下的力學要求。
2. 幾何尺寸精度檢測
通過激光測徑儀、超聲波測厚儀等設備測量鋼管外徑、壁厚、橢圓度及直線度。依據GB/T 3091《低壓流體輸送用焊接鋼管》規范,公差控制需精確至±0.5%以內,以保證裝配精度和動平衡性能。
3. 焊縫質量檢測
采用超聲波探傷(UT)和X射線探傷(RT)技術,檢測焊縫區域的未熔合、氣孔、夾渣等缺陷。焊縫強度需通過橫向拉伸試驗驗證,確保焊接接頭強度不低于母材的90%。
4. 表面質量與防腐檢測
利用目視檢查、磁粉探傷(MT)和渦流探傷(ET)排查表面裂紋、劃痕等缺陷。防腐涂層需按照ISO 21809進行附著力測試和鹽霧試驗,驗證其耐腐蝕性能。
5. 化學成分分析
通過光譜分析儀測定C、Mn、Si、S、P等元素含量,確保符合GB/T 699《優質碳素結構鋼》或客戶特定合金成分要求,避免材料脆性過高或加工硬化問題。
6. 耐疲勞性能測試
模擬傳動軸實際工況進行旋轉彎曲疲勞試驗,記錄鋼管在循環載荷下的裂紋萌生周期及斷裂壽命,驗證其抗疲勞性能是否達到設計標準。
檢測流程與質量控制
檢測過程需遵循“原料入場檢驗-生產過程抽檢-成品全檢”的三階管控模式。對于批量生產的電焊鋼管,采用統計過程控制(SPC)技術分析關鍵參數波動,確保質量一致性。檢測數據應實時錄入MES系統,實現全生命周期可追溯。
結語
傳動軸用電焊鋼管的檢測是保障機械傳動系統可靠性的基礎環節。通過多維度、多技術的綜合檢測手段,能夠全面評估鋼管性能并降低潛在風險。隨著智能制造技術的發展,基于AI的自動化檢測設備和數字孿生技術將進一步推動檢測效率與精度的提升。

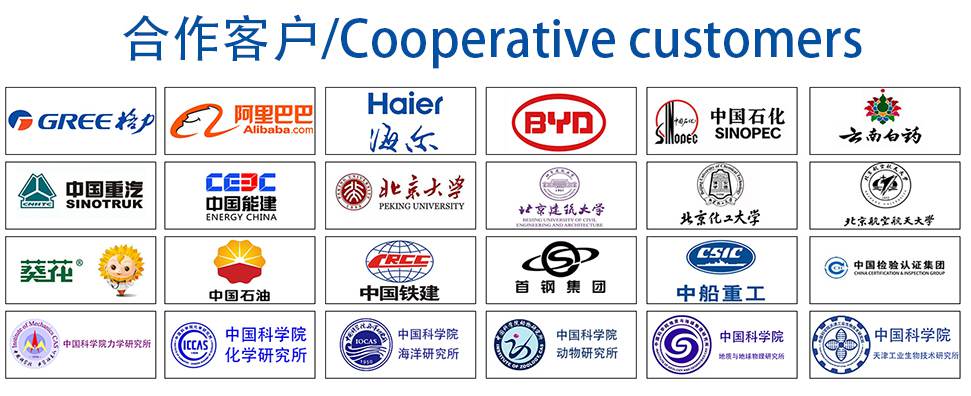