自動褲襻縫紉單元檢測技術解析
隨著服裝制造業自動化程度的提升,自動褲襻縫紉單元作為褲裝生產線的核心設備,其穩定性與精度直接影響成衣質量和生產效率。為確保設備高效運行并滿足工業化生產需求,系統性檢測成為設備調試、維護和優化的重要環節。現代檢測技術融合了機器視覺、傳感器反饋和數字化控制,能夠從機械性能、縫制質量、智能化水平等多個維度對設備進行全面評估。以下將圍繞自動褲襻縫紉單元的核心檢測項目展開詳細闡述。
關鍵檢測項目及技術要點
1. 機械結構穩定性檢測
重點評估縫紉機頭、送料機構及驅動系統的運行狀態。通過振動傳感器采集設備空載和滿載時的振幅數據,對比行業標準判斷機械磨損程度;利用激光對準儀檢測針桿與送料牙的垂直度誤差,精度需控制在±0.05mm以內。同步檢查傳動皮帶張緊度和齒輪嚙合狀況,防止跳針或斷線問題。
2. 縫制質量閉環檢測
采用工業相機配合圖像分析算法,實時監測線跡密度(通常要求18-22針/英寸)、縫線張力(標準值1.5-2.5N)及接縫平整度。對褲襻拐角處進行拉力測試(≥200N保持10秒),驗證接縫強度是否達標。同時通過色差儀檢測縫線與面料顏色匹配度,確保美觀性。
3. 智能控制系統驗證
模擬不同工況測試PLC程序的響應能力,包括緊急停機反應時間(≤0.1秒)、自動換線成功率(≥99.5%)及花樣縫制軌跡精度。使用示波器分析伺服電機驅動信號波形,核查加減速曲線的平滑性。特別需驗證視覺定位系統的重復定位精度(誤差≤0.1mm)。
進階性能與安全性檢測
4. 安全聯鎖裝置測試
對防護罩開閉感應、斷針檢測、過載保護等安全模塊進行500次以上連續觸發測試,要求功能失效率為零。通過注入干擾信號驗證控制系統抗電磁干擾能力,確保設備在復雜工業環境下穩定運行。
5. 能耗與效率綜合評價
記錄單位產量下的電能消耗(標準工況下≤0.8kW·h/百件),同時采用高速攝像機分析單件縫制周期時間(目標值≤6秒/件)。通過對比設備理論產能與實際產出數據,計算綜合設備效率(OEE),要求基準值≥85%。
數據化檢測體系構建
現代檢測需建立數字化檔案系統,通過RS485或以太網接口實時采集設備運行參數,結合MES系統實現質量追溯。關鍵數據包括針位偏移量歷史記錄、電機溫升曲線、異常事件代碼等,為預測性維護提供數據支撐。通過SPC統計過程控制方法,持續優化設備性能參數,推動生產質量持續改進。

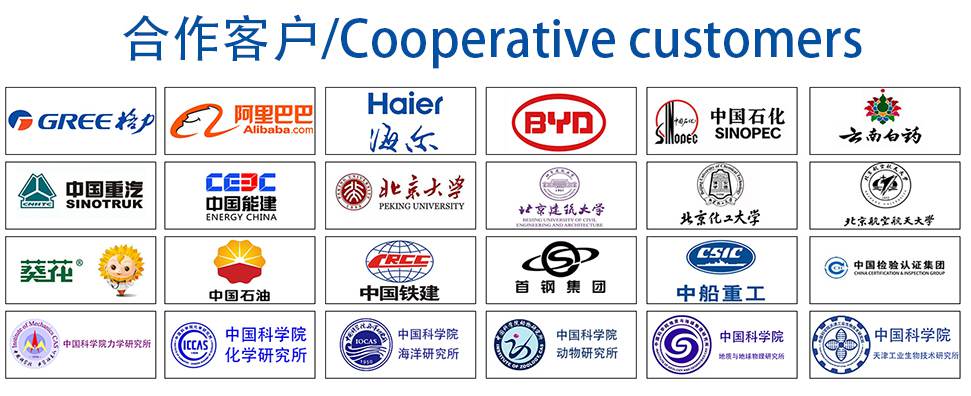