氣門檢測的重要性
氣門作為內燃機核心部件之一,其性能直接影響發動機的燃燒效率、動力輸出及排放指標。在高溫、高壓和高頻沖擊的工作環境中,氣門長期承受機械應力和熱應力雙重影響,易出現磨損、變形、積碳、燒蝕等故障。通過系統化的氣門檢測,可精準評估其密封性、幾何精度及材料完整性,對預防發動機異常磨損、功率下降及尾氣超標等問題具有關鍵作用。
主要檢測項目及方法
1. 氣門密封性檢測
采用煤油滲透法或專用氣密性測試儀,檢查氣門與座圈接觸面的密封效果。專業設備可量化泄漏率,標準要求應≤15ml/min。對于渦輪增壓發動機,需進行高溫工況下的動態密封測試。
2. 氣門外觀檢查
使用10倍放大鏡或工業內窺鏡檢測氣門頭部、桿部及鎖夾槽區域,重點關注:
- 頭部燒蝕凹坑深度(標準值≤0.2mm)
- 桿部直線度偏差(允許范圍0.02-0.05mm)
- 密封帶寬度均勻性(通常1.0-1.8mm)
3. 尺寸精度測量
應用三坐標測量儀、千分尺等工具檢測:
- 氣門總長度公差(±0.1mm)
- 桿部直徑偏差(標準H7/g6配合)
- 錐面角度誤差(多數機型要求45°±15')
4. 材料性能測試
通過金相分析檢測滲氮層深度(0.05-0.15mm)、硬度梯度(表面HV≥800),使用磁粉探傷檢查微觀裂紋,確保材料耐熱性(最高承受溫度:進氣門600℃,排氣門850℃)。
5. 動態特性分析
在氣門試驗臺上模擬實際工況,監測:
- 落座沖擊力(典型值200-400N)
- 運動軌跡偏差(≤0.1mm)
- 彈簧共振頻率(避開發動機常用轉速區間)
檢測周期建議
普通乘用車建議每6萬公里進行系統檢測,柴油發動機縮短至3萬公里。對于競技車輛或渦輪增壓機型,檢測頻率應提高30%。通過建立完整的檢測數據庫,可實現氣門壽命預測和預防性維護策略優化。

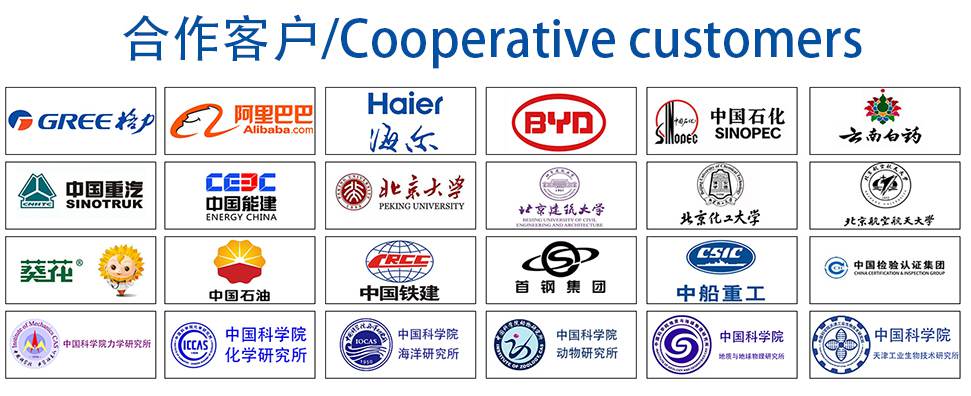