鋰離子蓄電池及蓄電池組檢測的重要性及核心項目解析
隨著新能源產業的快速發展,鋰離子蓄電池作為電動汽車、儲能系統及消費電子領域的核心動力源,其安全性、穩定性和循環壽命備受關注。據行業統計,2023年鋰離子電池市場規模已突破1200億美元,但與之相關的質量事故發生率仍呈現上升趨勢。在此背景下,專業的鋰離子蓄電池及蓄電池組檢測已成為保障產品性能、預防安全隱患的關鍵環節,檢測結果直接影響著終端產品的市場競爭力和用戶信任度。
核心檢測項目體系
1. 電性能測試
通過充放電測試系統模擬實際使用場景,精確測量容量保持率(循環500次后≥80%)、能量密度(≥150Wh/kg)、內阻值(<30mΩ)等關鍵指標。采用恒流恒壓(CC-CV)充電法和脈沖放電法評估電池動態響應特性,確保電池組在快速充放電條件下的穩定性。
2. 安全性能測試
依據GB 31241-2022強制標準,執行包括過充/過放測試(1.5倍額定電壓)、短路試驗(<5mΩ)、針刺試驗(鋼針直徑3mm)等極端工況模擬。特別針對熱失控傳播特性,要求電池組在單體故障時具備1小時以上的熱擴散防護能力。
3. 環境適應性測試
在溫度沖擊箱中執行-40℃至85℃循環測試,驗證電解液低溫結晶和高溫分解特性。85%RH高濕環境下持續720小時,檢測殼體密封性和極片腐蝕狀況。振動測試模擬車輛實際工況,施加頻率5-200Hz的隨機振動,持續3小時無結構損傷。
4. 機械性能測試
5. 壽命評估測試
通過加速老化試驗臺,在45℃高溫環境下進行1C倍率循環測試,建立容量衰減模型。采用電化學阻抗譜(EIS)分析界面SEI膜生長規律,預測電池組壽命衰減拐點。對于儲能系統用電池,需滿足>6000次循環(80%DoD)的使用要求。
檢測技術發展趨勢
隨著AI診斷技術的應用,最新檢測設備已實現云端數據比對和故障預判功能。X射線斷層掃描(CT)技術可無損檢測極片對齊度,精度達到微米級。國際電工委員會(IEC)最新發布的62660-3標準,已將硅基負極材料的膨脹率檢測納入強制項目,推動檢測技術持續升級。
專業的鋰離子蓄電池檢測體系,不僅需要覆蓋從單體到模組的全鏈條測試,更要結合應用場景建立差異化的評價標準。隨著固態電池等新技術的產業化推進,檢測項目將向著更高精度、更嚴苛條件的方向發展,為新能源行業的高質量發展提供技術保障。

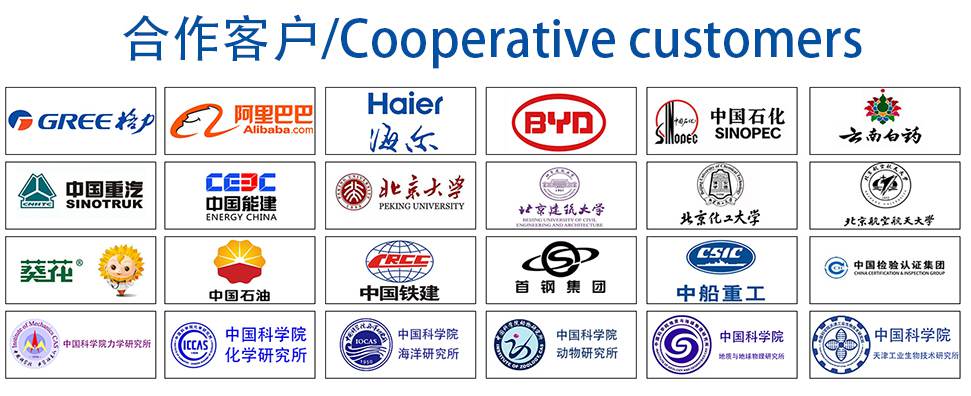