自潤滑襯套檢測的重要性及核心項目解析
自潤滑襯套作為機械設備中降低摩擦、延長使用壽命的關鍵部件,廣泛應用于汽車、航空航天、工程機械等領域。其核心功能在于通過內置固體潤滑劑或特殊復合材料結構,在無外部潤滑條件下實現持續減摩效果。然而,由于工作環境復雜多變(如高溫、高壓、腐蝕性介質等),對自潤滑襯套的性能檢測顯得尤為重要。系統化的檢測不僅能驗證產品質量,更能為設計優化和失效分析提供數據支撐,確保其在極端工況下的可靠性。
核心檢測項目分類與實施要點
1. 結構與尺寸公差檢測
使用三坐標測量儀、輪廓儀等設備,對襯套內/外徑、壁厚、圓度等關鍵尺寸進行精密測量,確保滿足±0.01mm的加工精度要求。同步檢測預埋潤滑劑的分布均勻性,避免因結構缺陷導致的局部磨損加劇。
2. 摩擦學性能評估
通過摩擦磨損試驗機模擬實際工況,測試動態摩擦系數(通常要求≤0.15)和PV值(壓力-速度乘積)極限。重點關注邊界潤滑條件下的性能穩定性,測試時長需覆蓋完整潤滑劑消耗周期。
3. 環境適應性測試
包含高溫(最高200℃)蠕變試驗、低溫(-40℃)脆性測試及鹽霧腐蝕試驗(按ASTM B117標準執行)。特殊應用場景還需進行真空環境或輻射條件下的材料性能退化評估。
4. 疲勞壽命與承載能力驗證
利用液壓伺服疲勞試驗機進行脈沖載荷測試(頻率5-20Hz),監測襯套在交變應力作用下的裂紋擴展情況。結合有限元分析,建立載荷-壽命曲線模型,為安全系數設定提供依據。
5. 材料成分與微觀結構分析
采用EDS能譜分析檢測基體金屬元素比例,SEM電鏡觀察潤滑相分布狀態。對燒結型襯套還需測定孔隙率(一般控制在15-25%),確保潤滑劑儲存與釋放的平衡。
6. 動態密封性能測試
針對密封型襯套設計專用試驗臺,在模擬介質(油/水/化學溶劑)中測試泄漏量,評估長期運行后的密封面磨損狀況。關鍵指標包括泄漏率(≤3ml/h)和往復運動百萬次后的性能保持率。
檢測標準體系與質量控制
行業檢測需嚴格遵循DIN 1494、ISO 3547等國際標準,同時結合GB/T 2889-2008等國內規范。企業應建立包含SPC統計過程控制的質控體系,對關鍵參數實施CPK≥1.33的過程能力管控,確保批量化生產的穩定性。
通過上述系統性檢測,可全面評估自潤滑襯套的機械性能、耐久性和環境適應性,為不同應用場景的選型提供科學依據。隨著智能傳感技術的發展,在線監測磨損狀態、溫度場分布等新型檢測手段正在推動行業向預測性維護方向升級。

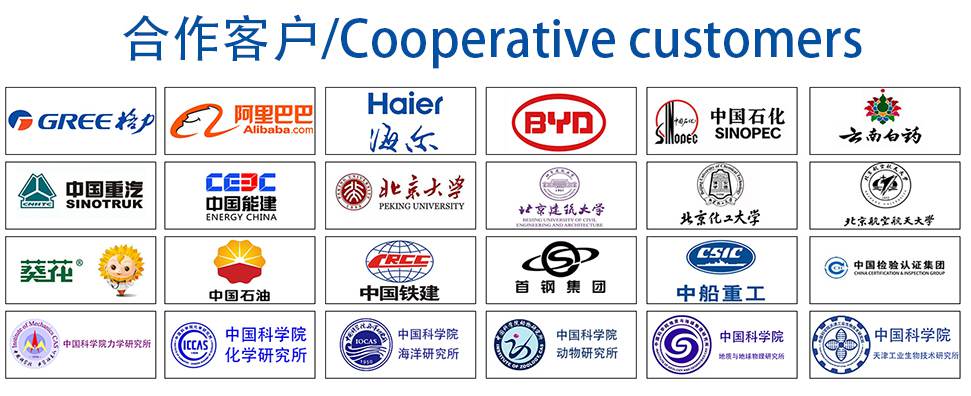