組合機床液壓滑臺檢測的重要性與核心項目
組合機床液壓滑臺作為機床的核心運動部件,其性能直接影響加工精度、生產效率及設備穩定性。液壓滑臺通過液壓驅動實現工件或刀具的直線運動,長期運行中易因油液污染、密封件磨損、系統壓力異常等問題導致動作遲緩、定位偏差或振動加劇。定期開展液壓滑臺檢測是保障設備高效運行、延長使用壽命的關鍵措施。檢測項目需覆蓋液壓系統、機械結構、控制元件及綜合性能,以全面評估滑臺的健康狀態,避免因部件失效引發停機事故。
一、液壓系統功能性檢測
1. 液壓壓力測試:使用壓力表檢測系統工作壓力是否達到設定值,觀察壓力波動是否在允許范圍內。異常壓力可能導致滑臺爬行或沖擊現象。
2. 泄漏檢測:檢查油缸、油管接頭及閥塊的密封性,通過目視或熒光檢漏劑排查外泄漏點,同時監測油溫變化判斷是否存在內泄漏。
3. 油液性能分析:采集液壓油樣本,檢測粘度、污染度(顆粒計數)及含水量,劣化油液會加速元件磨損并影響系統響應速度。
二、機械結構精度與磨損評估
1. 導軌磨損測量:使用千分表或激光干涉儀檢測導軌直線度、平行度及表面磨損量,超差會導致滑臺運動軌跡偏移。
2. 滑塊間隙檢測:通過塞尺測量滑塊與導軌接觸面間隙,過大的間隙會引發振動和精度損失。
3. 連接件剛性檢查:檢查滑臺與床身、驅動機構的連接螺栓預緊力,確保機械傳動的穩定性。
三、控制系統與傳感器校驗
1. 位置傳感器標定:使用光柵尺或磁柵尺校驗滑臺實際位移與反饋信號的匹配度,消除定位誤差。
2. 電磁閥響應測試:通過示波器監測電磁閥切換時間,滯后超過10%需更換閥體。
3. PLC程序邏輯驗證:模擬不同工況下的控制指令,確保滑臺啟停、調速及互鎖功能正常。
四、綜合性能驗收標準
完成單項檢測后需進行空載與負載試驗:
- 空載運行:滑臺全程移動速度波動≤±5%,無異常噪音或抖動。
- 負載測試:在額定載荷下重復定位精度應≤0.02mm,連續運行2小時油溫升幅不超過35℃。
通過系統性檢測可精準定位故障源,為液壓滑臺的維修或改造提供數據支撐,有效降低非計劃停機風險。

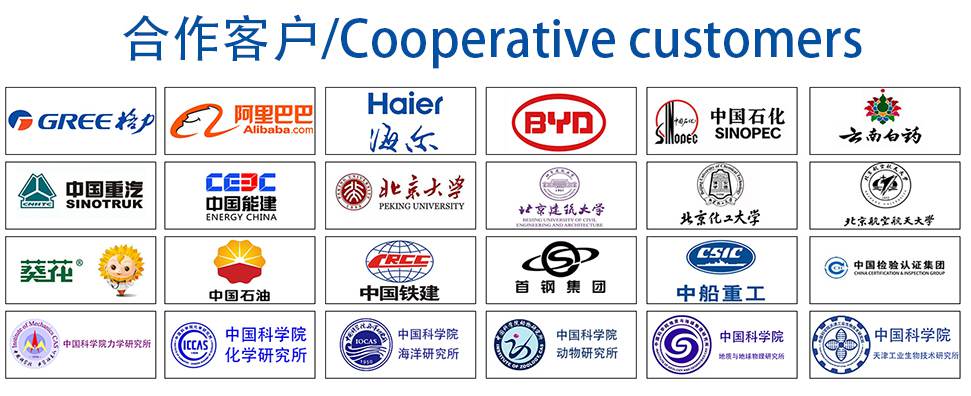