常壓容器檢測的必要性與應用背景
常壓容器是指設計壓力接近大氣壓(通常≤0.1MPa)的儲存或反應設備,廣泛應用于石油化工、制藥、食品加工、能源等行業,用于盛裝液體、氣體或混合介質。盡管其工作壓力較低,但長期運行中可能因腐蝕、疲勞、材料老化或操作不當導致結構損傷,甚至引發泄漏、爆炸等安全事故。因此,定期開展常壓容器檢測是確保企業安全生產、延長設備壽命、滿足國家法規(如《固定式壓力容器安全技術監察規程》)要求的重要手段。
常壓容器檢測的核心項目
1. 宏觀檢查與幾何尺寸測量
通過目視、放大鏡或內窺鏡檢查容器內外表面,識別變形、裂紋、鼓包、焊縫缺陷等異常現象。同時測量容器的直徑、橢圓度、壁厚等參數,評估是否符合設計規范。
2. 壁厚測定與腐蝕評估
使用超聲波測厚儀對容器關鍵部位(如底部、焊縫區、接管處)進行多點測量,分析壁厚減薄程度。結合歷史數據判斷腐蝕速率,預測剩余使用壽命。
3. 無損檢測(NDT)
包括以下方法: - 滲透檢測(PT):檢測表面開口裂紋; - 磁粉檢測(MT):適用于鐵磁性材料近表面缺陷; - 超聲檢測(UT):發現內部夾雜、分層等缺陷; - 射線檢測(RT):用于焊縫內部質量評估。
4. 安全附件與密封性檢查
驗證呼吸閥、液位計、溫度計等附件的功能有效性,并采用氣壓試驗或肥皂水法檢測接管法蘭、人孔等部位的密封性,防止介質泄漏。
5. 基礎與支撐結構檢查
檢查容器支座、地腳螺栓的腐蝕、變形情況,評估基礎沉降是否導致設備傾斜或應力集中,避免因支撐失效引發傾倒事故。
6. 材料性能分析(必要時)
對疑似劣化區域取樣進行金相分析、硬度測試或化學成分檢測,確認材料是否發生氫脆、硫化物應力腐蝕等變質現象。
檢測周期與結果處理
根據容器使用環境、介質特性及行業標準,檢測周期通常為3-6年。若發現嚴重缺陷(如貫穿性裂紋),需立即停用并制定修復或更換方案;輕度問題可通過補焊、加固等方式整改后繼續監控使用。
結語
常壓容器檢測是保障工業安全的核心環節,需結合多種技術手段實現全面評估。企業應建立完善的設備檔案,委托具備資質的檢測機構定期開展專業檢查,從源頭降低事故風險,實現安全與效益的雙重目標。

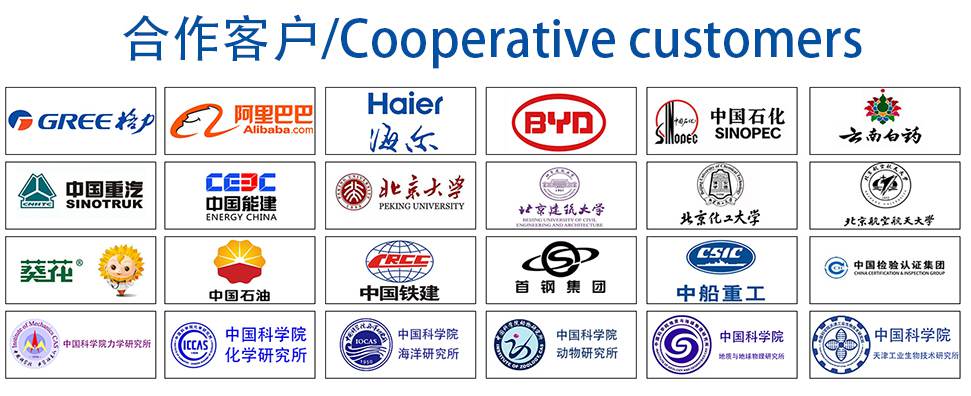