油管作為石油、天然氣等能源輸送的核心載體,其安全性與可靠性直接關(guān)系到工業(yè)生產(chǎn)效率和環(huán)境保護(hù)。隨著油管使用年限的增加,受腐蝕、磨損、焊接缺陷等因素影響,管道可能出現(xiàn)泄漏、破裂等安全隱患。因此,定期開展油管檢測成為保障能源運輸安全、延長管道壽命的重要手段。通過科學(xué)系統(tǒng)的檢測技術(shù),能夠精準(zhǔn)識別潛在風(fēng)險,為維護(hù)和修復(fù)提供數(shù)據(jù)支持,避免因管道失效引發(fā)的重大事故。
1. 油管壁厚檢測
壁厚檢測是油管檢測的基礎(chǔ)項目,主要通過超聲波測厚儀或射線檢測技術(shù)對管道的實際壁厚進(jìn)行測量。由于管道長期受介質(zhì)沖刷或腐蝕,壁厚會逐漸減薄,若低于安全閾值可能導(dǎo)致結(jié)構(gòu)性失效。檢測時需沿管道軸向和環(huán)向選取多點進(jìn)行測量,結(jié)合歷史數(shù)據(jù)評估腐蝕速率,為管道剩余壽命預(yù)測提供依據(jù)。
2. 腐蝕與損傷檢測
腐蝕是油管失效的主要誘因之一。檢測方法包括漏磁檢測(MFL)、超聲波C掃描(UT)以及紅外熱成像技術(shù)。漏磁檢測適用于發(fā)現(xiàn)管道內(nèi)外壁的腐蝕坑、裂紋等缺陷;超聲波技術(shù)可精確定量腐蝕深度;紅外熱成像則能快速識別局部溫度異常區(qū)域,輔助判斷腐蝕活躍部位。
3. 焊縫質(zhì)量檢測
油管焊接接頭是故障高發(fā)區(qū)域。檢測項目涵蓋X射線探傷、相控陣超聲波檢測(PAUT)和磁粉探傷。X射線可發(fā)現(xiàn)氣孔、夾渣等內(nèi)部缺陷,PAUT技術(shù)能對焊縫進(jìn)行三維成像,而磁粉檢測主要用于表面裂紋的識別。通過綜合手段確保焊縫強度符合API 5L等國際標(biāo)準(zhǔn)。
4. 壓力試驗與密封性檢測
通過水壓試驗或氣壓試驗驗證油管的承壓能力,通常要求加壓至設(shè)計壓力的1.5倍并保壓一定時間。同時采用氦氣檢漏、皂泡試驗或聲發(fā)射技術(shù)檢測微小泄漏點,確保管道在高壓工況下的密封性能。該檢測項目尤其適用于新建管線驗收或大修后的系統(tǒng)驗證。
5. 內(nèi)涂層完整性檢測
對采用內(nèi)防腐涂層的油管,需使用高清管道內(nèi)窺鏡(PIG)或電磁渦流檢測儀評估涂層破損情況。涂層剝落會導(dǎo)致基材直接接觸腐蝕介質(zhì),加速管道劣化。檢測結(jié)果將指導(dǎo)涂層修復(fù)方案,延長管道在酸性或高含水介質(zhì)中的使用壽命。
6. 地質(zhì)應(yīng)力與變形監(jiān)測
針對埋地油管,需通過慣性測繪(IMU)或分布式光纖傳感技術(shù)監(jiān)測管道因地基沉降、地震或第三方施工引起的形變。結(jié)合地理信息系統(tǒng)(GIS)數(shù)據(jù),分析應(yīng)力集中區(qū)域,及時采取加固措施避免彎曲斷裂風(fēng)險。
通過以上多維度的檢測項目,可構(gòu)建油管全生命周期的健康管理體系。現(xiàn)代檢測技術(shù)正朝著智能化、自動化的方向發(fā)展,如無人機巡檢、智能爬行機器人(Crawler)和數(shù)字孿生技術(shù)的應(yīng)用,將進(jìn)一步推動油管檢測的精準(zhǔn)性和效率,為能源運輸安全保駕護(hù)航。

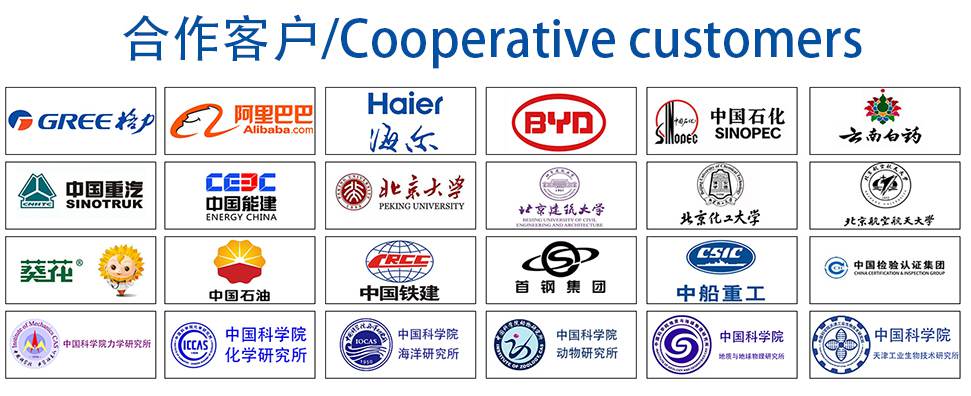