油氣井套管及油管用鋼管檢測的重要性
在石油天然氣勘探開發過程中,套管和油管作為井身結構的關鍵組成部分,承擔著支撐井壁、密封油氣層、傳輸介質等多重功能。由于長期承受高溫高壓、腐蝕性介質及復雜應力環境,其質量直接關系到油氣井的安全性、使用壽命和生產效率。通過科學規范的鋼管檢測,能夠有效發現材料缺陷、尺寸偏差和性能隱患,預防因管材失效導致的井噴、泄漏等重大事故,同時延長設備服役周期,保障油氣田開發的穩定性和經濟性。以下針對套管及油管用鋼管的核心檢測項目展開詳細說明。
一、材料性能檢測
材料性能是鋼管質量的基礎保障,主要檢測項目包括:
1. 化學成分分析:采用光譜儀或化學滴定法驗證碳、錳、鉻、鉬等元素含量是否符合API 5CT等標準要求;
2. 力學性能測試:通過拉伸試驗測定屈服強度、抗拉強度和延伸率,利用沖擊試驗評估低溫韌性,確保材料具備足夠的抗變形和抗斷裂能力;
3. 金相組織分析:觀察微觀晶粒結構,檢測是否存在偏析、夾雜物等冶金缺陷。
二、幾何尺寸與形位公差檢測
精確的尺寸控制是保障管材密封性和連接性能的關鍵:
1. 使用激光測徑儀或卡規測量外徑、壁厚及橢圓度,確保符合公差范圍;
2. 通過螺紋量規檢測接箍螺紋的螺距、錐度及緊密距,驗證螺紋加工精度;
3. 采用三維影像測量系統檢查管體直線度及端面垂直度,避免安裝過程中出現應力集中。
三、無損檢測技術應用
針對鋼管表面及內部缺陷的精準識別:
1. 超聲波檢測(UT):檢測管壁內部裂紋、分層等體積型缺陷,精度可達毫米級;
2. 磁粉檢測(MT):用于發現表面及近表面的磁性材料缺陷,如疲勞裂紋;
3. 渦流檢測(ET):快速篩查管材表面微小裂紋和腐蝕坑,適用于大批量生產檢測;
4. 射線檢測(RT):通過X射線或γ射線成像技術定位焊接區域的氣孔、未熔合等缺陷。
四、特殊工況性能驗證
針對特定作業環境的附加檢測需求:
1. 抗擠毀試驗:模擬高壓地層對套管的徑向擠壓力,測定臨界失穩壓力值;
2. 耐腐蝕試驗:通過鹽霧試驗、HIC(氫致開裂)試驗評估抗硫化氫腐蝕能力;
3. 高溫高壓密封性測試:在模擬井下環境中驗證螺紋連接的氣密封性能;
4. 疲勞壽命試驗:通過循環載荷測試預測鋼管在交變應力下的耐久性。
五、檢測標準的執行與認證
所有檢測項目均需嚴格遵循API 5CT、ISO 11960等國際標準,同時結合ASTM、GB/T等國家規范。第三方實驗室認證(如 、DNV)可確保檢測結果的權威性和度。通過建立完整的質量追溯體系,實現從原材料到成品管的全生命周期質量控制。
油氣井管材檢測技術的持續創新(如數字化檢測、AI缺陷識別)正在推動行業向更高安全等級和智能化方向發展。只有通過系統化、多維度的檢測手段,才能為深井、超深井及非常規油氣開發提供可靠的材料保障。

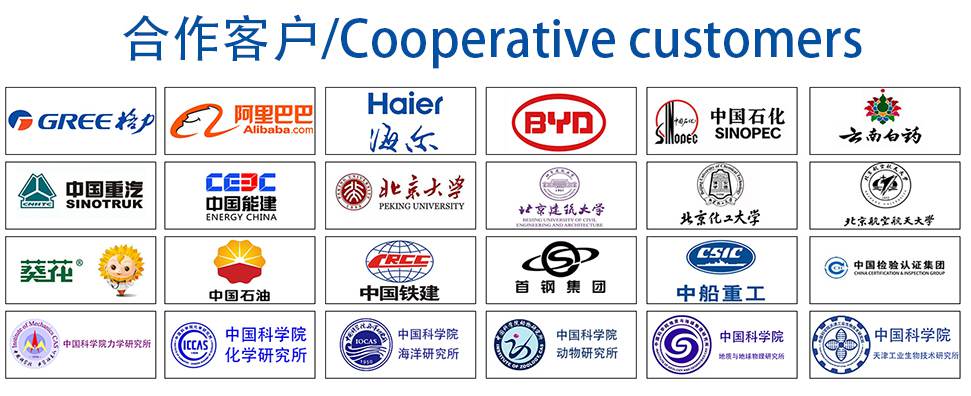