鈦及鈦合金無縫管檢測的核心價值與應用領域
鈦及鈦合金無縫管因其高強度、耐腐蝕、輕量化等優異性能,被廣泛應用于航空航天、石油化工、醫療植入器械、海洋工程等高端領域。這些場景對材料的質量要求極為嚴苛,任何微小的缺陷或成分偏差都可能導致設備失效甚至重大事故。為此,針對鈦及鈦合金無縫管的系統性檢測成為確保其性能穩定性和使用安全性的核心環節。通過科學的檢測手段,可精準驗證材料是否符合GB/T 3624-2010《鈦及鈦合金無縫管》等國家標準以及ASTM B338等國際規范要求,同時為生產工藝優化提供數據支撐。
關鍵檢測項目與技術解析
1. 化學成分分析
采用電感耦合等離子體發射光譜(ICP-OES)、X射線熒光光譜(XRF)等儀器,檢測鈦基體中鋁、釩、鐵、氧等元素的含量,確保合金成分滿足TA1、TA2、TC4等牌號的技術指標要求,避免雜質元素超標導致的晶間腐蝕風險。
2. 力學性能測試
通過萬能試驗機完成抗拉強度(≥895MPa)、屈服強度(≥825MPa)和延伸率(≥10%)測試,驗證管材在極端載荷下的形變能力;借助維氏硬度計(HV)和夏比沖擊試驗機,評估材料硬度(通常HV≥320)及低溫韌性(-196℃沖擊吸收功≥34J)。
3. 無損檢測(NDT)
綜合運用超聲波探傷(UT)檢測內部裂紋、氣孔等缺陷(靈敏度≤Φ1.6mm平底孔),渦流探傷(ET)檢測表面微裂紋,液體滲透檢測(PT)識別開口缺陷,以及X射線實時成像(DR)對焊縫和熱影響區進行三維缺陷定位。
4. 幾何尺寸與表面質量檢測
使用激光測徑儀測量外徑公差(±0.15mm),內窺鏡檢測內壁光潔度(Ra≤1.6μm),金相顯微鏡觀察晶粒度(ASTM E112標準6-8級),同時通過目視和涂層測厚儀驗證表面氧化層厚度(2-5μm)及是否存在劃痕、褶皺等表觀缺陷。
5. 耐腐蝕性驗證
通過鹽霧試驗(5% NaCl溶液,35℃持續720小時)、酸堿浸泡試驗(10% HCl、40% NaOH溶液,80℃下24小時)等方法評估耐蝕性,配合電化學工作站測定自腐蝕電位(Ecorr≥-0.25V)和點蝕擊穿電位(Eb≥1.0V),確保在海洋大氣或強腐蝕介質中的長期穩定性。
全流程質量控制的意義
完整的檢測體系需貫穿從原料熔煉到成品出廠的全生命周期:熔煉階段監控鑄錠成分均勻性,熱擠壓過程控制β相轉變溫度(TC4合金約995℃),冷軋工序跟蹤加工硬化率,熱處理后檢測相組成(α+β雙相組織占比),最終通過爆破試驗(1.5倍工作壓力保壓30秒)驗證承壓能力。只有嚴格執行各環節檢測標準,才能確保鈦管在超臨界機組、艦船冷凝器等高壓高溫場景下的可靠性。

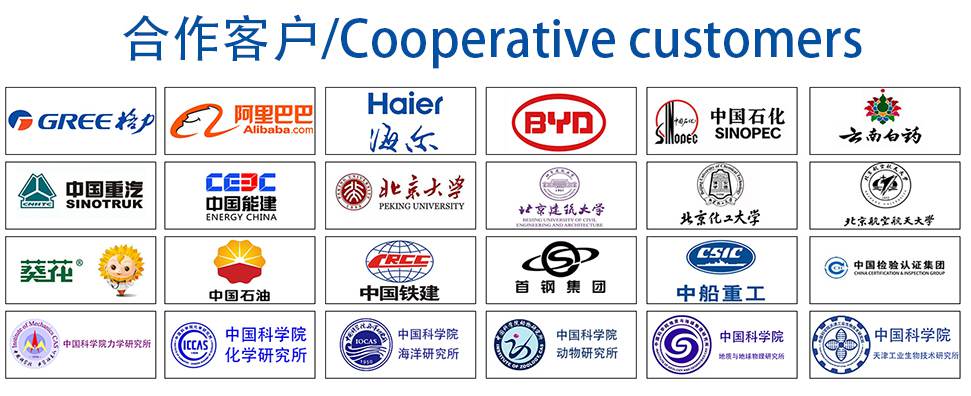