航空機輪用鈦合金異型鍛件檢測的關鍵意義
隨著航空航天技術的飛速發(fā)展,鈦合金因其高強度、耐腐蝕、輕量化等優(yōu)異性能,成為航空機輪等關鍵部件的首選材料。異型鍛件作為航空機輪的核心承力結構,其形狀復雜、受力工況嚴苛,對材料性能和制造工藝提出了極高要求。為確保航空器運行安全,針對鈦合金異型鍛件的檢測需覆蓋原材料性能、成型工藝質量以及服役可靠性三大維度,貫穿從生產到應用的全生命周期。本文將圍繞檢測項目展開詳細解析,闡明各環(huán)節(jié)的技術要點與行業(yè)標準。
主要檢測項目與技術方法
1. 材料成分與力學性能檢測
鈦合金異型鍛件的化學成分需嚴格符合航空級標準(如AMS 4928)。通過直讀光譜儀(OES)或X射線熒光分析(XRF)驗證鈦基體中鋁、釩等合金元素的含量,同時檢測氧、氮、氫等雜質元素的限值。力學性能測試包括室溫/高溫拉伸試驗、沖擊韌性試驗及硬度測試,確保鍛件在極端環(huán)境下的抗拉強度(≥900MPa)和延伸率(≥10%)達標。
2. 幾何尺寸與形位公差檢測
采用三坐標測量機(CMM)或激光掃描儀對異型鍛件的三維輪廓進行數(shù)字化比對,重點檢測法蘭盤厚度、輪轂內徑、螺栓孔位置度等關鍵尺寸,偏差需控制在±0.1mm以內。對于非對稱結構的流線型設計部位,需通過有限元分析(FEA)驗證應力分布與理論模型的一致性。
3. 內部缺陷無損檢測
通過超聲波探傷(UT)和工業(yè)CT掃描檢測鍛件內部的氣孔、夾雜、裂紋等缺陷。根據(jù)NAS 410標準,超聲探頭頻率選擇5-10MHz,缺陷當量直徑需≤0.8mm。對于復雜曲面區(qū)域,需采用相控陣超聲(PAUT)技術實現(xiàn)多角度掃查,確保檢測盲區(qū)覆蓋率≥99%。
4. 表面質量與耐腐蝕性評估
使用熒光滲透檢測(FPT)或磁粉檢測(MT)檢查表面微裂紋,配合金相顯微鏡觀察α+β雙相組織的均勻性。鹽霧試驗(ASTM B117)模擬海洋大氣環(huán)境,要求鍛件經(jīng)720小時測試后無點蝕或晶間腐蝕現(xiàn)象,表面氧化膜厚度應維持在2-5μm范圍內。
5. 殘余應力與疲勞壽命測試
采用X射線衍射法測定鍛件關鍵部位的殘余應力分布,梯度變化不得超過材料屈服強度的20%。通過高頻疲勞試驗機(R≥0.1)進行107次循環(huán)加載試驗,結合斷口SEM分析,驗證鍛件在交變載荷下的裂紋擴展抗性,目標壽命需超過設計要求的1.5倍安全系數(shù)。
檢測標準與質量控制體系
航空機輪鍛件的檢測需嚴格遵循AS9100D航空質量管理體系,同時參照AMS 2380(鈦合金鍛件驗收標準)、MIL-STD-2154(超聲檢測規(guī)程)等專項規(guī)范。企業(yè)需建立全流程追溯系統(tǒng),實現(xiàn)從原材料熔煉批次到成品檢測數(shù)據(jù)的數(shù)字化管理,確保每個鍛件的檢測報告包含至少50項關鍵參數(shù)的可視化圖譜。
結語
鈦合金異型鍛件的檢測是保障航空安全的重要防線。隨著增材制造、智能傳感等新技術的應用,檢測體系正朝著自動化、高精度、多參量融合的方向發(fā)展。未來,基于機器學習的缺陷識別算法與數(shù)字孿生技術的深度結合,將進一步提升航空鍛件質量控制的智能化水平。

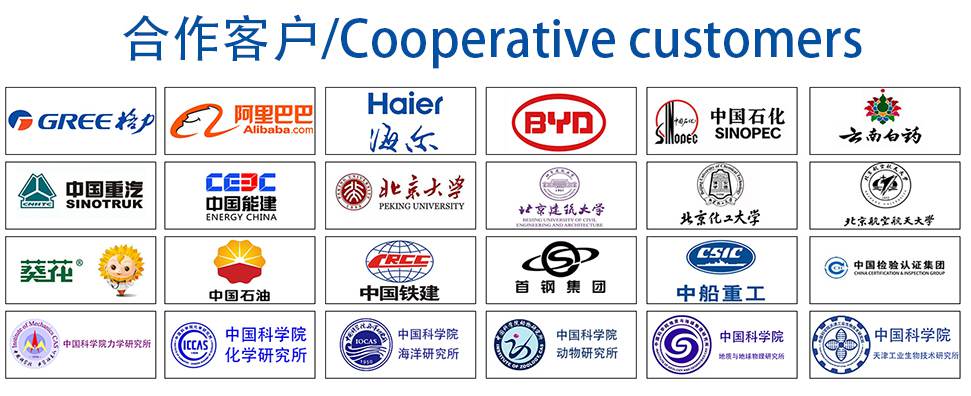