航空用鈦及鈦合金板材和帶材檢測的重要性
隨著航空工業的快速發展,鈦及鈦合金因其高強度、耐腐蝕、耐高溫和低密度的特性,成為飛機結構件、發動機零部件等關鍵部位的首選材料。航空用鈦合金板材和帶材的質量直接影響飛行器的安全性和使用壽命,因此必須通過嚴格的檢測流程確保其性能符合適航標準。檢測項目覆蓋從原材料成分到成品的全方位質量控制,涉及物理性能、化學成分、微觀組織以及表面缺陷等多個維度。只有通過科學規范的檢測手段,才能保障材料在極端環境下的可靠性和穩定性。
核心檢測項目與技術要求
1. 化學成分分析
鈦合金的力學性能與耐腐蝕性與其化學成分密切相關。通過光譜分析(如ICP-OES、X射線熒光光譜)和燃燒法,檢測鈦基體中鋁、釩、鐵、氧等元素的含量是否符合GB/T 3620.1、AMS 4911等標準要求。特別是雜質元素(如氫、碳)的超標可能引發氫脆或脆性斷裂,需嚴格控制在允許范圍內。
2. 力學性能測試
包括拉伸試驗(抗拉強度、屈服強度、延伸率)、沖擊韌性測試、硬度測試(布氏/洛氏硬度)及彎曲試驗等。例如按照ASTM E8/E8M標準,板材需在橫向和縱向取樣,模擬實際載荷下的力學響應。高溫條件下的持久強度和蠕變性能也是航空材料檢測的重點。
3. 微觀組織檢驗
通過金相顯微鏡或掃描電鏡(SEM)觀察鈦合金的晶粒度、相組成(α相、β相分布)及夾雜物含量。依據GB/T 5168標準,均勻細小的晶粒結構可提升材料的疲勞壽命,而異常粗大晶粒或偏析會導致應力集中,需判定為不合格品。
4. 無損檢測
采用超聲波檢測(UT)篩查板材內部裂紋、分層缺陷;渦流檢測(ET)識別表面及近表面的微小缺陷;滲透檢測(PT)用于定位開口型裂紋。根據AMS 2631標準要求,缺陷尺寸超過0.5mm需進行復檢或報廢處理。
5. 尺寸精度與形位公差
使用激光測距儀、三坐標測量機等設備檢測板材和帶材的厚度偏差、平面度、邊緣直線度等參數。航空級鈦材對厚度公差的控制通常要求在±0.05mm以內,以確保裝配精度和結構強度。
6. 耐腐蝕性測試
通過鹽霧試驗(ASTM B117)、應力腐蝕試驗(ASTM G39)評估材料在海洋大氣或高溫高壓環境下的抗腐蝕能力。部分航空鈦合金還需進行氧化膜致密性檢測,防止高溫氧化導致的性能退化。
7. 工藝性能驗證
包括成形性試驗(如杯突試驗)、焊接接頭性能測試及熱處理后的性能復驗,確保材料在加工過程中不會出現開裂、回彈異常等問題。例如超薄帶材需通過反復彎曲試驗驗證其柔韌性。
航空用鈦及鈦合金的檢測貫穿原材料入廠到成品出廠的全流程,需結合齊全儀器與標準化操作流程,為航空器的安全飛行構筑堅實的技術防線。

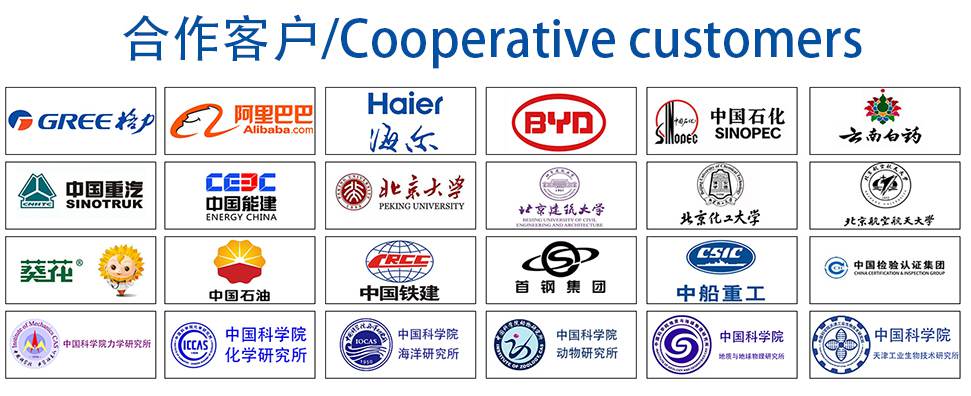