向心滾針和保持器組件作為滾動軸承的核心部件,廣泛應用于汽車變速箱、工業減速器、航空航天等高精度傳動系統中,其性能直接影響設備的承載能力、旋轉精度及使用壽命。為確保組件在高速、重載工況下的可靠性,需通過系統性檢測驗證其幾何精度、材料性能、裝配質量等關鍵指標。檢測流程需嚴格遵循ISO 3030、GB/T 309-2017等行業標準,結合目視檢查、尺寸測量、材料分析及動態試驗等手段,全面評估組件在疲勞壽命、抗磨損性和抗變形能力等方面的表現。
一、外觀與尺寸精度檢測
采用3D光學輪廓儀與電子顯微鏡對滾針表面進行100%全檢,識別劃痕、凹坑、銹蝕等缺陷。保持器需重點檢測兜孔形狀公差(±0.02mm)、窗梁厚度偏差(≤±5%),使用三坐標測量儀驗證節圓直徑(PCD)的徑向跳動量(≤0.03mm)。滾針直徑分組需達到微米級精度,確保同一組內直徑差≤1μm。
二、材料性能測試
通過洛氏硬度計(HRC 58-62)檢測滾針表面硬化層深度(0.6-1.2mm),采用光譜儀分析GCr15軸承鋼的化學成分(Cr含量1.45%-1.65%)。保持器需進行鹽霧試驗(96小時無紅銹)驗證鍍鋅層防腐性,注塑保持器應通過DSC差示掃描量熱法檢測PA66材料的玻璃化轉變溫度(≥220℃)。
三、裝配配合特性檢測
使用軸向游隙儀測量組件裝配后的軸向間隙(0.02-0.08mm),保持器與滾針的徑向配合間隙需控制在0.05-0.15mm。動態檢測包含:
- 扭矩測試:空載啟動力矩≤0.15N·m
- 溫升試驗:3000rpm持續運轉2小時溫升≤35℃
- 振動值檢測:加速度有效值≤1.5m/s2
四、耐久性驗證試驗
在專用試驗臺上進行加速壽命測試,施加額定動載荷(Cr值)的120%進行100萬次循環,檢測保持器兜孔磨損量(≤0.01mm)、滾針表面剝落面積(≤0.5%)。同時開展極限轉速試驗,記錄保持器塑性變形時的臨界轉速值(需≥標稱轉速的150%)。
企業應建立檢測數據追溯系統,建議每季度進行預防性檢測,重點監控保持器窗梁應力集中區域。通過實施SPC統計過程控制,可將組件早期故障率降低60%以上,顯著延長軸承使用壽命。

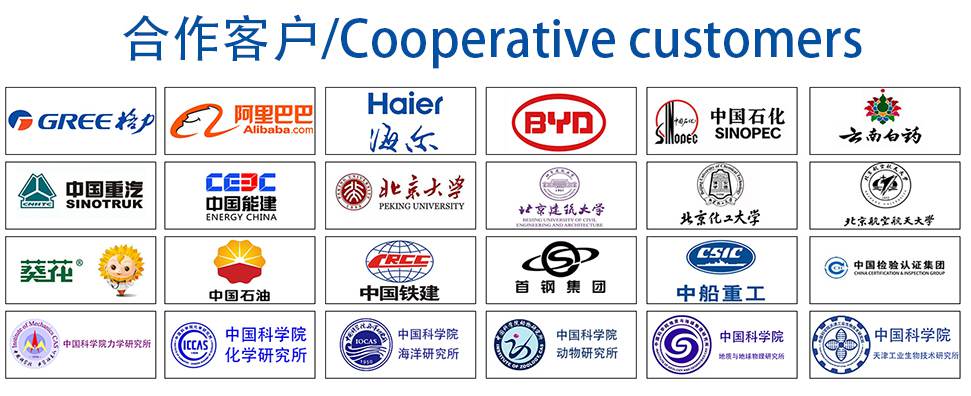