軸承座檢測:全面把控機械基礎件質量的核心環節
在機械傳動系統中,軸承座作為承載和固定軸承的關鍵部件,其質量直接影響到設備的運行精度、使用壽命及安全性。隨著現代工業對設備可靠性要求的不斷提升,軸承座檢測已成為機械制造和維保過程中的重要質量控制環節。專業化的檢測體系不僅能夠及時發現生產缺陷,更能通過數據化分析為產品優化提供科學依據,確保軸承座在復雜工況下保持穩定的支撐性能和精準的配合特性。
核心檢測項目體系
1. 尺寸精度檢測
使用三坐標測量儀、投影儀等精密儀器,對安裝孔徑、同軸度、平行度、垂直度等關鍵尺寸進行三維檢測。重點驗證軸承座內孔直徑公差是否滿足H7級精度要求,定位止口與安裝面的垂直度誤差控制在0.02mm/m以內。
2. 表面質量檢測
通過目視檢查配合磁粉探傷,檢測鑄造或機加工表面是否存在裂紋、氣孔、砂眼等缺陷。使用表面粗糙度儀測量關鍵配合面的Ra值,確保軸承安裝面粗糙度≤1.6μm,油封接觸面≤3.2μm。
3. 材料性能測試
采用光譜分析儀進行材料成分驗證,確保符合HT250/GG25等牌號要求。通過布氏硬度計檢測本體硬度(180-240HB),沖擊試驗機驗證材料韌性,金相分析評估鑄件石墨形態及基體組織。
4. 配合特性檢測
使用液壓拉伸裝置模擬軸承壓裝過程,檢測過盈配合的軸向壓裝力曲線。采用激光對中儀測量軸承座與軸系的同軸度,確保徑向跳動量≤0.05mm,端面跳動≤0.03mm。
5. 密封性能測試
對帶密封結構的軸承座進行IP防護等級測試,使用氣壓檢漏儀檢測防塵防水性能。潤滑系統接口需經受1.5倍工作壓力的保壓試驗,30分鐘內壓力降不超過5%。
6. 動態性能驗證
在專用試驗臺上進行模擬工況測試,監測高速運轉時的振動值(≤4.5mm/s)、溫升變化(ΔT≤35℃)及噪音水平。通過200小時耐久試驗評估疲勞強度,檢測微動磨損和變形情況。
智能化檢測發展趨勢
當前行業正加速推進數字化檢測技術應用,基于機器視覺的自動尺寸檢測系統可實現100%在線全檢,檢測效率提升3倍以上。結合大數據分析的預測性質量控制系統,能夠實時監控生產波動,自動優化加工參數。采用相控陣超聲檢測技術,可精確識別鑄件內部3mm以上缺陷,檢測精度較傳統方法提高40%。
科學的檢測體系應建立全過程質量追溯機制,從原材料入廠到成品出廠形成完整的檢測數據鏈。建議企業參照ISO/TS 16949標準建立檢測規范,結合工況特點制定分級檢測方案,在保證質量可靠性的同時實現成本最優配置。

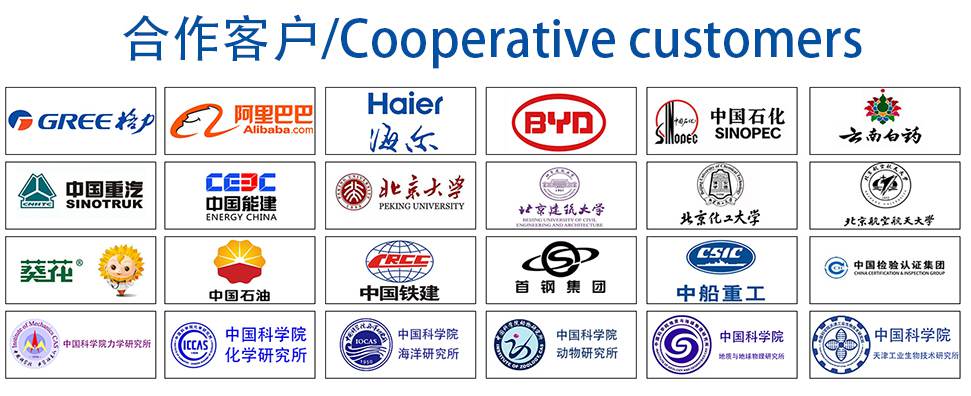