軋機壓下機構用滿裝圓錐滾子推力軸承檢測的重要性
在冶金軋制設備中,軋機壓下機構是控制軋輥間距的核心組件,其運行穩定性直接關系到板材軋制精度和設備使用壽命。作為關鍵傳動部件的滿裝圓錐滾子推力軸承,需承受高軸向載荷、沖擊載荷及復雜工況下的交變應力。針對此類軸承開展系統化檢測,不僅能預防突發性故障導致的停機損失,還可通過數據積累優化設備維護周期,顯著降低生產成本。尤其對于連續作業的軋機產線,軸承的微小缺陷可能引發連鎖反應,因此建立完善的檢測體系具有重要工程價值。
核心檢測項目及技術要求
1. 外觀與表面質量檢測
采用10倍放大鏡與工業內窺鏡對滾道、滾子、保持架進行目視檢查,重點識別疲勞剝落、壓痕、擦傷等缺陷。檢測標準需滿足ISO 15243:2017中定義的表面損傷等級要求,對于寬度超過0.5mm的連續劃痕或深度超過0.02mm的壓痕應視為不合格。
2. 尺寸精度校驗
使用激光測徑儀和三維坐標測量機檢測軸承內外圈直徑公差、滾子錐角偏差及總高度波動量。按GB/T307.1規定,軸向游隙應控制在0.08-0.15mm范圍內,徑向圓跳動不得超過0.03mm/m,端面平行度偏差需≦0.02mm。
3. 材料性能分析
通過洛氏硬度計(HRC標尺)檢測滾道表面硬度,要求達到58-62HRC的硬化層深度。采用金相顯微鏡觀察材料微觀組織,確保馬氏體含量≥95%、殘余奧氏體≯5%,避免出現碳化物偏析或異常晶粒長大現象。
4. 潤滑狀態評估
利用油液光譜分析儀檢測潤滑油脂的金屬磨損顆粒濃度,配合鐵譜分析判斷異常磨損類型。要求40μm以上磨粒數≤100個/ml,潤滑劑酸值變化不超過初始值的15%。同時通過紅外熱像儀監測軸承運行溫度,異常溫升不得超過環境溫度+45℃。
5. 動態性能測試
在專用試驗臺上模擬實際工況,測量軸承在額定轉速下的振動加速度值(RMS)。根據ISO10816-3標準,振動烈度應低于4.5mm/s,頻譜分析中不得出現明顯的倍頻或邊帶異常頻率成分。
6. 極限載荷試驗
采用分級加載方式測試軸承破壞強度,要求軸向靜載能力達到標稱值的1.5倍時無永久變形,2.2倍載荷下保持30分鐘不出現結構性失效。動態疲勞壽命試驗需滿足ISO281標準中L10壽命≥8000小時的要求。
檢測數據綜合管理
建立包含歷史檢測數據、工況參數、維修記錄的數據庫,運用大數據分析技術預測軸承剩余壽命。對于關鍵軋機設備,建議每500小時進行在線監測,每2000小時實施全面離線檢測。通過SPC控制圖監控關鍵參數變化趨勢,當接觸角偏差超過0.5°或游隙變化量達初始值20%時,應立即啟動預防性維護程序。
結語
針對軋機用滿裝圓錐滾子推力軸承的特殊工況,構建包含機械性能、材料特性、動態響應的多維檢測體系,是實現設備預知性維護的關鍵。通過融合傳統檢測手段與智能診斷技術,可顯著提升軸承可靠性,為冶金企業創造可觀的經濟效益。檢測過程中需特別注意環境溫度補償、測量基準統一等細節,確保數據真實反映軸承的實際工作狀態。

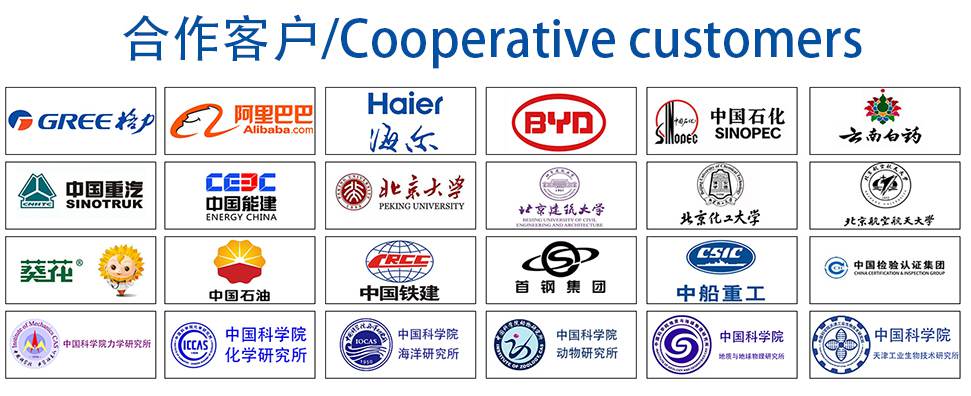