張緊輪與惰輪軸承及其單元檢測的重要性
在機械傳動系統中,張緊輪和惰輪是確保皮帶或鏈條傳動平穩運行的核心組件。張緊輪通過調節皮帶的張緊力來減少打滑和振動,而惰輪則用于改變傳動路徑或支撐中間段的傳動帶。兩者的核心部件——軸承及其單元的性能直接決定了輪體的使用壽命和傳動效率。若軸承出現磨損、腐蝕或潤滑失效,輕則導致噪音增大、能耗上升,重則引發傳動系統故障甚至停機。因此,對張緊輪和惰輪軸承單元的定期檢測與維護至關重要。
檢測項目與技術要求
1. 外觀與尺寸精度檢測
通過目視檢查軸承表面是否存在劃痕、銹蝕或變形,并使用三坐標測量儀檢測輪體安裝孔位、軸承座尺寸是否符合設計公差(通常要求誤差≤0.02mm)。重點檢查密封圈是否完好,防止潤滑脂泄漏和外部污染物侵入。
2. 旋轉靈活性測試
在無負載條件下,測試軸承單元的旋轉扭矩和空轉阻力。采用扭矩傳感器量化數據(標準值一般≤0.3N·m),異常阻力可能表明內部滾珠磨損或潤滑不足。同步監測旋轉時的異響,判斷是否存在卡滯問題。
3. 振動與噪音分析
使用振動頻譜儀和聲級計采集軸承在模擬工況下的振動加速度值(通常要求≤5m/s2)及噪音分貝(≤65dB)。通過頻譜特征識別異常頻率,如高頻尖峰可能對應滾道損傷,低頻波動則可能由裝配偏移引起。
4. 密封性能驗證
將軸承單元置于高溫(80℃以上)和高濕度(RH≥90%)環境中,進行連續72小時的密封性試驗。檢測潤滑脂流失量(標準應<3%),并觀察是否有水汽滲入導致的乳化現象。
5. 材料與熱處理檢驗
通過金相顯微鏡分析軸承鋼的顯微組織,確認熱處理工藝是否達標(如GCr15鋼的硬度需在HRC60-64之間)。針對高負荷工況,還需進行X射線衍射(XRD)檢測表面滲碳層厚度(推薦≥0.8mm)以評估抗疲勞強度。
6. 動態性能測試
在專用試驗臺上模擬實際工況,測試軸承單元在極限轉速(如10000rpm)下的溫升(應≤80℃)和穩定性。結合有限元分析(FEA)軟件,驗證應力分布是否均勻,避免局部過載導致的早期失效。
7. 壽命評估與失效預測
采用ISO 281標準中的修正壽命公式L10= (C/P)^p,結合實際載荷譜計算理論壽命。同時開展加速壽命試驗(如3倍額定負載循環測試),統計磨損量隨時間的變化曲線,建立預防性維護周期模型。
總結
張緊輪與惰輪軸承單元的檢測需覆蓋從微觀材料特性到宏觀動態性能的多維度參數。通過標準化檢測流程與智能診斷技術的結合,可顯著提升故障預警能力,降低傳動系統非計劃停機風險。企業應結合設備工況制定分級檢測策略,確保關鍵部件在生命周期內高效可靠運行。

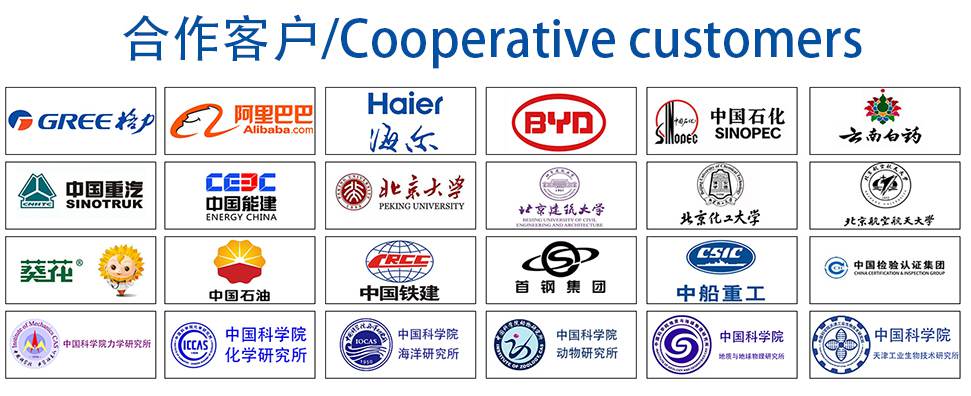